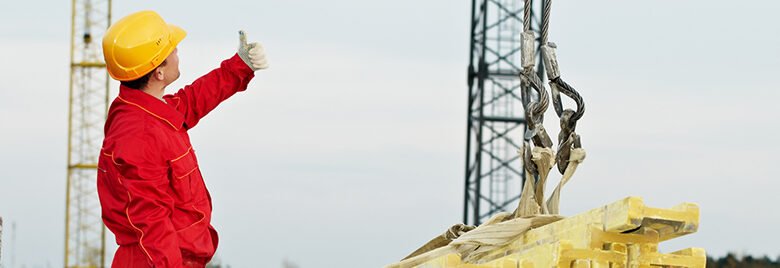
Handling corrosive chemicals is a critical concern in various industries, necessitating stringent safety protocols to protect workers. Corrosive chemicals can cause severe damage to living tissues and materials, making their handling a high-risk activity. Understanding these risks is crucial for ensuring workplace safety and compliance with regulatory standards. This is where an OSHA Course becomes invaluable. The Occupational Safety and Health Administration (OSHA) provides comprehensive guidelines and training programs, such as the OSHA Course, to educate workers and employers about the safe handling of hazardous substances.
Completing an OSHA Course equips individuals with the necessary knowledge and skills to manage corrosive chemicals safely, mitigating potential hazards. Furthermore, obtaining an OSHA Certificate demonstrates a commitment to maintaining a safe working environment, which is essential for both legal compliance and the well-being of employees.
Understanding Corrosive Chemicals
1. What Are Corrosive Chemicals?
Corrosive chemicals are substances that can cause destruction of living tissue or material upon contact. These include acids, bases, and other chemicals capable of causing chemical burns, respiratory issues, and other severe health effects. Common examples include hydrochloric acid, sulfuric acid, sodium hydroxide, and ammonia.
2. Common Uses of Corrosive Chemicals
Corrosive chemicals are used across a wide range of industries, including manufacturing, pharmaceuticals, cleaning, and water treatment. They play vital roles in processes such as etching, cleaning, neutralization, and pH adjustment.
Health Risks Associated with Corrosive Chemicals
1. Immediate Health Effects
- Skin Contact: Direct contact with corrosive chemicals can cause severe burns, blisters, and permanent tissue damage. Immediate washing and decontamination are critical.
- Eye Contact: Splashing corrosive substances into the eyes can result in serious injuries, including blindness. Immediate flushing with water is necessary to minimize damage.
- Inhalation: Breathing in vapors or fumes from corrosive chemicals can lead to respiratory distress, irritation of the mucous membranes, and long-term lung damage.
- Ingestion: Swallowing corrosive substances can cause severe internal injuries, including burns to the mouth, throat, and digestive tract.
2. Long-term Health Effects
Prolonged or repeated exposure to corrosive chemicals can lead to chronic health conditions such as dermatitis, respiratory issues, and other organ damage. Regular medical surveillance and health monitoring are essential for workers in environments with continuous exposure.
Safety Measures and Precautions
1. Personal Protective Equipment (PPE)
Using appropriate PPE is crucial when handling corrosive chemicals. This includes:
- Gloves: Resistant to the specific chemical being handled.
- Eye Protection: Safety goggles or face shields to prevent splashes.
- Respirators: To protect against inhalation of harmful vapors.
- Protective Clothing: Lab coats, aprons, or full-body suits to prevent skin contact.
2. Engineering Controls
Implementing engineering controls can significantly reduce the risk of exposure. These include:
- Ventilation Systems: Proper ventilation and fume hoods to disperse harmful vapors.
- Safety Showers and Eyewash Stations: Accessible in areas where corrosive chemicals are used.
- Spill Containment: Adequate systems to manage and contain accidental spills.
3. Administrative Controls
Administrative controls involve procedural measures to enhance safety, such as:
- Training and Education: Completing an OSHA Course ensures that employees are well-versed in the proper handling and emergency procedures for corrosive chemicals. This training is essential for obtaining an OSHA Certificate.
- Standard Operating Procedures (SOPs): Detailed protocols for safely managing and disposing of corrosive substances.
- Labeling and Signage: Clear labeling of chemical containers and appropriate hazard warnings.
Emergency Response and First Aid
1. Immediate Response Actions
In the event of an accidental exposure to corrosive chemicals, quick and effective action can mitigate injury severity. Key steps include:
- Skin Contact: Remove contaminated clothing and rinse the affected area with water for at least 15 minutes.
- Eye Contact: Flush eyes with water for at least 15 minutes and seek medical attention immediately.
- Inhalation: Move to fresh air immediately and seek medical assistance if symptoms persist.
- Ingestion: Do not induce vomiting. Rinse the mouth with water and seek immediate medical help.
2. Emergency Preparedness
Being prepared for emergencies involves:
- Emergency Plans: Developing and practicing response plans for chemical spills and exposures.
- First Aid Training: Ensuring that employees are trained in first aid specific to chemical injuries.
- Access to Medical Facilities: Having arrangements with nearby medical facilities for rapid response and treatment.
Regulatory Compliance and Training
1. OSHA Standards and Guidelines
OSHA has established specific standards and guidelines for the safe handling of hazardous chemicals, including corrosives. Adhering to these standards is not only a legal requirement but also a best practice for ensuring workplace safety.
2. The Role of OSHA Courses
An OSHA Course provides comprehensive training on the safe handling, storage, and disposal of corrosive chemicals. It covers:
- Hazard Communication: Understanding Safety Data Sheets (SDS) and proper labeling.
- Chemical Storage: Guidelines for segregating incompatible chemicals and ensuring proper storage conditions.
- Personal Protective Equipment: Selection, use, and maintenance of PPE.
- Spill Response and Cleanup: Procedures for managing accidental releases.
3. Obtaining an OSHA Certificate
Completing an OSHA Course and obtaining an OSHA Certificate signifies that an individual has met the necessary training requirements and is competent in handling corrosive chemicals safely. This certification enhances workplace safety and demonstrates compliance with regulatory standards.
Best Practices for Handling Corrosive Chemicals
1. Storage and Handling
- Proper Storage: Store corrosive chemicals in well-ventilated areas, away from incompatible substances, and in appropriate containers.
- Handling Techniques: Use secondary containment, such as trays, when transferring chemicals to prevent spills.
2. Disposal of Corrosive Chemicals
- Waste Management: Follow local regulations for the disposal of hazardous waste. Never pour corrosive chemicals down the drain unless specifically permitted.
- Neutralization: Neutralize acids and bases before disposal when possible, following safety guidelines.
3. Continuous Improvement and Monitoring
- Regular Inspections: Conduct routine inspections of storage areas and PPE to ensure they are in good condition.
- Safety Audits: Perform regular safety audits to identify and address potential hazards.
- Employee Feedback: Encourage employees to report safety concerns and suggest improvements.
Conclusion
Working with corrosive chemicals poses significant safety risks, but with proper training, protective measures, and adherence to regulatory guidelines, these risks can be effectively managed. Completing an OSHA Course and obtaining an OSHA Certificate are critical steps in ensuring that workers are knowledgeable about safe handling practices and emergency response procedures. By fostering a culture of safety and continuous improvement, organizations can protect their employees, comply with legal requirements, and maintain a safe working environment.