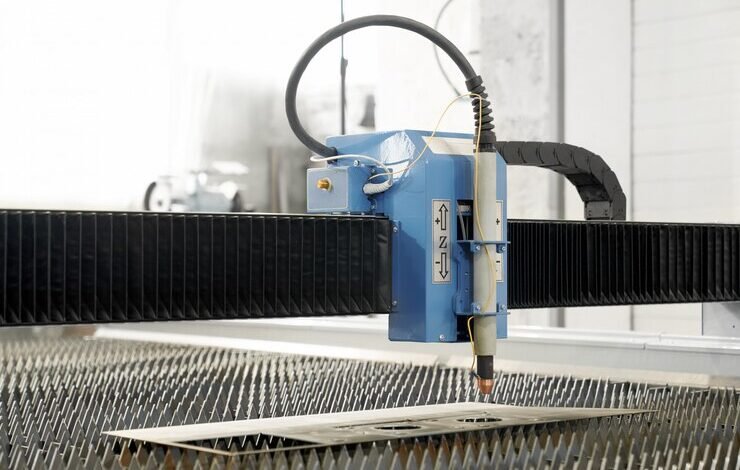
Introduction
A CNC Tool Probe is an essential component in modern CNC machining. It is a device used to measure the position and dimensions of tools in CNC machines, ensuring that they are correctly aligned and functioning accurately. The primary purpose of a CNC Tool Probe is to enhance precision, reduce setup time, and improve the overall efficiency of CNC operations.
Benefits of Using a Tool Probe
Using a CNC Tool Probe offers numerous advantages in the machining process:
- Enhanced Precision: Tool probes provide accurate measurements, ensuring that the tools are perfectly positioned. This precision translates to higher quality finished products.
- Reduced Setup Time: With a tool probe, the time required to set up CNC machines is significantly reduced. This efficiency allows for quicker transitions between tasks and increased productivity.
- Improved Efficiency: The automation of tool measurement and alignment through a tool probe minimizes human error, leading to smoother and more efficient operations.
Types of Tool Probes
There are various types of CNC Tool Probes, each designed for specific applications:
- Touch Probes: These probes physically touch the tool to measure its position. They are commonly used for tool setting and workpiece inspection.
- Laser Probes: Laser probes use laser beams to measure tool dimensions without physical contact. They are ideal for delicate tools that might be damaged by touch probes.
- Optical Probes: These probes use optical sensors to detect the tool’s position and dimensions. They are highly accurate and suitable for precision tasks.
Installation and Setup
Installing and setting up a CNC Tool Probe involves several steps:
- Mounting the Probe: Attach the probe to the CNC machine following the manufacturer’s instructions. Ensure it is securely fixed to avoid any movement during operation.
- Calibration: Calibrate the probe by aligning it with a known reference point. This step ensures that the measurements taken by the probe are accurate.
- Integration with CNC Software: Configure the CNC machine’s software to recognize and utilize the tool probe. This integration allows the machine to automatically adjust settings based on the probe’s measurements.
Common Applications
CNC Tool Probes are particularly beneficial in various scenarios:
- Tool Setting: Probes are used to set the precise position of tools before machining begins, ensuring accuracy from the start.
- Workpiece Inspection: After machining, probes can inspect the workpiece to verify that it meets the required specifications.
- Tool Wear Monitoring: Probes can regularly check tools for wear and tear, allowing for timely replacements and maintaining machining quality.
Maintenance and Troubleshooting
Proper maintenance and troubleshooting are crucial for the optimal performance of a CNC Tool Probe:
- Regular Cleaning: Keep the probe clean to prevent debris from affecting its accuracy.
- Periodic Calibration: Regularly recalibrate the probe to maintain its precision.
- Troubleshooting Issues: If the probe malfunctions, check for loose connections, misalignment, or software configuration errors. Address these issues promptly to minimize downtime.
Conclusion
Incorporating a CNC Tool Probe into CNC operations significantly enhances precision, reduces setup time, and improves efficiency. By understanding the types of tool probes, their installation and setup, and maintaining them properly, manufacturers can achieve higher quality and productivity in their machining processes. The importance of tool probes in the realm of CNC operations cannot be overstated.