Synthetic Gypsum Manufacturing Plant Project Report 2024: Industry trends and Plant Setup
Synthetic Gypsum Manufacturing Plant Project Report
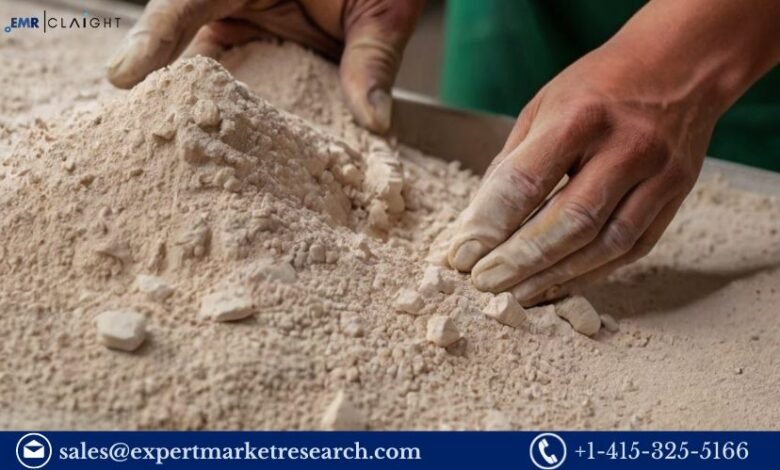
Introduction
Synthetic gypsum, primarily produced as a byproduct of industrial processes, has gained popularity as an alternative to natural gypsum in various applications, particularly in construction. Known for its eco-friendly properties and versatility, synthetic gypsum is extensively used in the production of drywall, cement, and as a soil amendment. This Synthetic Gypsum Manufacturing Plant Project Report details the establishment of a synthetic gypsum manufacturing plant, outlining market demand, production processes, financial considerations, and potential environmental impacts.
Market Overview
Growing Demand for Synthetic Gypsum
The global synthetic gypsum market is experiencing robust growth, driven by rising construction activities, sustainability initiatives, and increasing awareness of environmental issues. According to industry forecasts, the synthetic gypsum market is expected to grow at a CAGR of approximately 7% over the next five years. Key factors contributing to this growth include:
- Increased Construction Activities: As urbanization accelerates, the demand for drywall and plasterboard continues to rise.
- Sustainability Trends: Companies are increasingly seeking eco-friendly alternatives to natural gypsum to reduce their environmental footprint.
- Agricultural Applications: Synthetic gypsum is also being used as a soil amendment to improve soil quality and reduce erosion.
Target Markets
- Construction Industry: Major consumers include manufacturers of drywall and plaster products.
- Cement Production: Used as a mineral additive in cement to regulate setting time.
- Agriculture: Applied to enhance soil health and improve crop yield.
Get a Free Sample Report with Table of Contents @
Project Objectives
The primary objective of establishing a synthetic gypsum manufacturing plant is to meet the growing market demand while ensuring high-quality production. Key goals include:
- Production Capacity: Initial target of producing 50,000 tons of synthetic gypsum annually.
- Quality Assurance: Adherence to international quality standards, such as ISO 9001.
- Sustainability: Implementing eco-friendly practices throughout the manufacturing process.
Manufacturing Process
1. Raw Material Sourcing
The primary raw materials for synthetic gypsum production include:
- Flue Gas Desulfurization (FGD) Gypsum: A byproduct from the combustion of fossil fuels in power plants.
- Chemical Additives: Depending on the desired properties of the final product.
Sourcing high-quality materials is essential to ensure the effectiveness and purity of synthetic gypsum.
2. Gypsum Production
The production of synthetic gypsum involves the following steps:
- Collection of FGD Gypsum: The gypsum byproduct is collected from flue gas desulfurization systems used in coal-fired power plants.
- Purification: The collected gypsum is purified to remove impurities and ensure compliance with quality standards.
- Drying: The gypsum is dried to reduce moisture content, making it suitable for use in construction applications.
3. Milling and Processing
Once dried, the gypsum is milled to achieve the desired particle size. This process may include:
- Grinding: Reducing the gypsum to a fine powder for improved performance in applications.
- Mixing: Adding any necessary chemical additives to enhance specific properties.
4. Quality Control
Implementing rigorous quality control measures is crucial for ensuring the final product meets industry standards. This includes:
- Testing: Regular testing of raw materials and finished products for purity, strength, and performance.
- Compliance: Adhering to regulations set by industry standards organizations.
5. Packaging and Distribution
The final product is packaged in bulk bags or smaller quantities, depending on customer requirements. Effective logistics and distribution channels are essential for reaching target markets.
Financial Considerations
Initial Investment
Setting up a synthetic gypsum manufacturing plant requires substantial capital investment, including:
- Land and Facility: Acquiring land and constructing a facility equipped for production.
- Machinery: Purchasing specialized equipment for drying, milling, and processing gypsum.
- Working Capital: Funds needed for raw materials, labor, and operational expenses during the initial phase.
Funding Sources
Potential funding sources for the project may include:
- Bank Loans: Traditional financing options for manufacturing ventures.
- Venture Capital: Attracting investors interested in sustainable building materials.
- Government Grants: Exploring funding opportunities aimed at promoting eco-friendly initiatives.
Financial Projections
A robust financial model should project revenues, expenses, and profits over a five-year period. Factors influencing profitability include production efficiency, pricing strategies, and market demand.
Environmental Impact
Sustainable Practices
Establishing a synthetic gypsum manufacturing plant allows for the incorporation of sustainable practices, such as:
- Waste Reduction: Utilizing industrial byproducts, thereby reducing landfill waste.
- Energy Efficiency: Employing energy-efficient machinery and processes.
- Pollution Control: Implementing measures to minimize emissions and environmental impact.
Compliance
Compliance with environmental regulations is essential. Conducting environmental impact assessments (EIAs) and obtaining necessary permits will ensure responsible manufacturing practices and promote sustainability.
FAQs
1. What is synthetic gypsum?
Synthetic gypsum is a byproduct created from industrial processes, particularly flue gas desulfurization, and is used as a substitute for natural gypsum in construction and agriculture.
2. What are the main applications of synthetic gypsum?
Synthetic gypsum is primarily used in the production of drywall, cement, and as a soil amendment in agriculture to improve soil quality.
3. How is synthetic gypsum produced?
Synthetic gypsum is produced by collecting flue gas desulfurization gypsum, purifying it, drying it, and milling it to achieve the desired particle size.
4. Is synthetic gypsum environmentally friendly?
Yes, synthetic gypsum is considered environmentally friendly as it utilizes industrial byproducts, reducing waste and the need for natural gypsum extraction.
5. What are the regulatory requirements for synthetic gypsum production?
Manufacturers must comply with quality standards such as ISO 9001 and environmental regulations to ensure safe and responsible production practices.
Related Reports
https://www.expertmarketresearch.com/reports/packaged-food-market/companies
https://www.expertmarketresearch.com/reports/polystyrene-market
https://www.expertmarketresearch.com/reports/data-centre-outsourcing-market
Media Contact:
Company Name: Claight Corporation
Contact Person: Lewis Fernandas, Corporate Sales Specialist — U.S.A.
Email: sales@expertmarketresearch.com
Toll Free Number: +1–415–325–5166 | +44–702–402–5790
Address: 30 North Gould Street, Sheridan, WY 82801, USA
Website: www.expertmarketresearch.com
Aus Site: https://www.expertmarketresearch.com.au