The Right Equipment for Efficient Mild Steel Fabrication
Discover essential equipment for efficient mild steel fabrication. Learn the tools needed for precise cutting, shaping, welding, and safe handling.
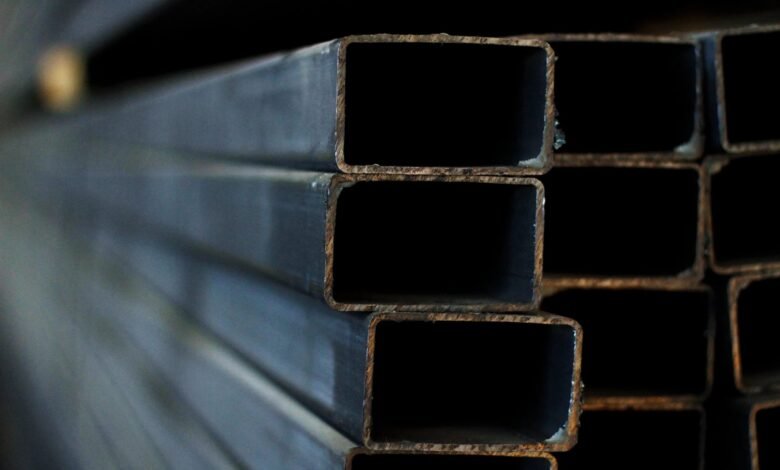
Mild steel fabrication involves cutting, bending, and shaping mild steel into various designs. Mild steel is a top choice because of its affordability and versatility. Industries like construction, automotive, and manufacturing use it often. However, working with mild steel requires the right equipment to ensure quality and efficiency. Without proper tools, the process becomes slow, costly, and risky. This guide covers the essential equipment needed for efficient mild steel fabrication. Each tool has a specific purpose to make the job smoother and safer.
Understanding Mild Steel
Before discussing tools, it’s important to know what mild steel is. Mild steel, also known as low-carbon steel, has a lower carbon content than other steels (typically 0.05% to 0.25%). This makes mild steel easier to bend, shape, and weld. It’s perfect for applications that don’t need extremely high strength but do require flexibility and durability.
Because of these qualities, mild steel is a favorite for many fabrication projects. To handle it efficiently, though, the right equipment is essential.
Essential Equipment for Mild Steel Fabrication
Each step in fabricating mild steel requires specific tools for accuracy and safety. Here are the key tools used in the process:
1. Cutting Tools
Cutting is usually the first step in mild steel fabrication. This stage involves shaping the steel into smaller, workable sizes. Some common cutting tools are:
- Band Saws: Designed for making straight cuts in thicker steel. They’re quick and produce clean edges.
- Plasma Cutters: These use hot plasma to melt and cut through the steel. Plasma cutting is fast and efficient.
- Laser Cutters: Laser cutters allow for precise, intricate designs. However, they can be more costly than other options.
Using the right cutting tool ensures the job is easy and precise. Accurate cuts are critical in projects that require exact dimensions.
2. Bending and Shaping Tools
After cutting, the steel often needs bending or shaping. Bending tools help create the right angles or curves for each design.
- Press Brakes: These machines apply pressure to bend the steel at specific angles. Press brakes come in both hydraulic and manual options.
- Rolling Machines: Rolling machines are used for creating rounded shapes in steel. They can form cylindrical shapes with precision.
- Tube and Pipe Benders: Special benders are used for mild steel pipes and tubes. They bend the material without damaging its structure.
These tools help achieve the desired shapes while preserving the steel’s strength and structure.
3. Welding Equipment
Welding is a crucial part of steel fabrication. This step joins steel pieces to create a strong structure. Different welding methods are used depending on the project.
- MIG Welders: MIG welding is ideal for mild steel. It’s easy to handle and creates clean, strong welds.
- TIG Welders: TIG welding is more precise, resulting in smooth, neat welds. However, it’s slower and requires skill.
- Arc Welders: This method is often used for thicker steel. It produces strong welds, though it may need some cleanup afterward.
Using the right welding tool is essential to achieve strong, clean joints.
Additionaly see: Pre-Engineered Buildings: Why Indian Companies Choose Them
4. Finishing Tools
After cutting, bending, and welding, the steel usually needs finishing. This stage improves the appearance and safety of the final product.
- Grinders: Grinders smooth rough edges and remove excess weld. They come in various types, like angle grinders and bench grinders.
- Sanders and Polishers: Sanders gives mild steel a smooth finish, which is important for projects where appearance matters. Polishers add a shiny, professional look.
- Deburring Tools: These tools remove sharp edges or burrs left from cutting and welding. This step is important for safety.
Finishing tools ensure the steel piece is polished, smooth, and safe for use.
5. Measuring and Inspection Tools
Precision is key in mild steel fabrication. Even small errors can impact the final product’s quality. Measuring tools help avoid these mistakes.
- Calipers and Micrometers: These tools measure the thickness and dimensions of the steel accurately. They ensure consistency across parts.
- Squares and Levels: Used to check angles and alignment. These tools are essential for shaping steel accurately.
- Weld Gauges: Weld gauges measure the quality of the welds. They help ensure that welds are strong and secure.
Accurate measurements prevent costly errors and improve quality.
Safety Equipment for Mild Steel Fabrication
Safety is crucial when working with mild steel. The process involves heavy machinery, high temperatures, and sharp edges. Essential safety equipment includes:
- Safety Glasses: Protects eyes from sparks and debris during cutting, grinding, and welding.
- Gloves: Heat-resistant gloves protect hands from burns.
- Ear Protection: Fabrication can be loud, so ear protection helps prevent hearing damage.
- Welding Helmets and Respirators: Helmets protect the face and eyes from bright light and sparks. Respirators are needed in enclosed spaces with fumes.
Safety equipment reduces risks and allows fabricators to focus on precision and quality.
Why the Right Equipment Matters
Choosing the right equipment for mild steel fabrication improves efficiency. It also impacts the quality of the final product. For example, accurate cutting tools reduce material waste. Bending tools help create consistent shapes that fit well with other components. Good welding equipment ensures durable joints. Finishing tools polish the product, improving its appearance and safety.
Investing in quality equipment also boosts productivity. With the right tools, workers complete tasks faster and with fewer errors. Safety equipment also reduces the risk of accidents, creating a safe work environment that supports high-quality work.
Conclusion
Efficient mild steel fabrication in Delhi NCR requires various tools, from cutting and bending to finishing and measuring. Each piece of equipment plays a role in achieving strength, precision, and quality in the final product. When fabricators choose the right tools and prioritize safety, they produce reliable, long-lasting products from mild steel.
Using the right equipment for mild steel fabrication is essential for quality and durability. The metal’s versatility makes it ideal for countless applications, and with the right tools, fabricators handle each step with ease and accuracy. By staying updated with the latest advancements, they not only improve production efficiency but also enhance the overall quality of their work. This commitment to excellence ensures that every mild steel structure or component is built to meet high industry standards, making them suitable for various applications in construction, manufacturing, and more.
Also see: India’s Road Construction Boom: What’s Driving the Surge?