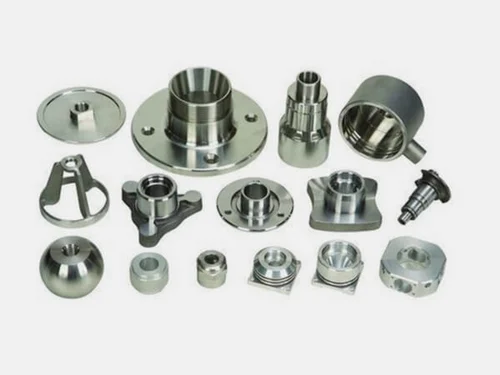
In the dynamic landscape of aerospace manufacturing, India has emerged as a significant hub for aerospace components manufacturers. The country’s expertise in engineering, coupled with a robust industrial ecosystem, has propelled several companies to the forefront of this specialized industry. Let’s delve deeper into the insights from aerospace components manufacturers in India.
Aerospace Components Manufacturers in India: A Growing Presence
Aerospace components manufacturers in India play a crucial role in the global supply chain, catering to both domestic and international markets. Companies like BVPL Turbine Parts are leading this charge, leveraging advanced technologies and skilled manpower to produce high-quality components for aircraft and spacecraft.
Innovation and Technology: Driving Factors
One key aspect that sets Indian aerospace manufacturers apart is their focus on innovation and technology. These companies continually invest in research and development to enhance product quality, reduce costs, and meet stringent industry standards. BVPL Turbine Parts, for instance, pioneers cutting-edge manufacturing techniques to produce precision-engineered components.
Quality Standards and Certifications
Adherence to international quality standards and certifications is paramount in aerospace manufacturing. Indian aerospace components manufacturers maintain rigorous quality control processes to ensure compliance with regulations set by bodies like the International Organization for Standardization (ISO) and the Aerospace Industries Association (AIA). BVPL Turbine Parts upholds these standards to deliver reliable and safe components to its clients.
Skilled Workforce: A Competitive Advantage
India’s rich pool of engineering talent is another driving force behind the success of aerospace components manufacturers. These professionals are adept at handling complex manufacturing processes and are quick to adapt to new technologies. BVPL Turbine Parts employs skilled engineers and technicians who contribute to the company’s reputation for excellence.
Challenges and Opportunities
Despite the growth trajectory, the aerospace manufacturing sector in India faces certain challenges. These include the need for infrastructure development, regulatory complexities, and global competition. However, these challenges also present opportunities for continuous improvement and expansion within the industry.
Future Outlook
The future looks promising for aerospace components manufacturers in India. With increasing investments in infrastructure and technology, coupled with government initiatives such as Make in India and the liberalization of foreign direct investment (FDI) norms, the sector is poised for significant growth.
Conclusion
In conclusion, the insights from aerospace components manufacturers in India highlight the industry’s evolution and potential. Companies like BVPL Turbine Parts exemplify the commitment to innovation, quality, and excellence that define India’s aerospace manufacturing sector.
Frequently Asked Questions
What is aerospace component manufacturing?
Aerospace component manufacturing refers to the process of designing, engineering, and producing parts and assemblies used in aircraft and spacecraft. These components can range from simple parts like bolts and brackets to complex systems such as engines, avionics, and structural elements. Aerospace component manufacturing involves precision engineering and adheres to stringent quality and safety standards to ensure the reliability and performance of aerospace vehicles.
Key aspects of aerospace component manufacturing include:
- Design and Engineering: Aerospace components are designed using advanced CAD (Computer-Aided Design) software and engineering principles to meet specific performance requirements and safety standards. The design phase considers factors like aerodynamics, structural integrity, and material properties.
- Materials Selection: Aerospace components are typically manufactured using lightweight and high-strength materials such as aluminum alloys, titanium, composites, and advanced polymers. Material selection is critical to achieving optimal performance while minimizing weight and cost.
- Manufacturing Processes: Aerospace components are produced using various manufacturing processes including machining, forming, casting, forging, welding, and additive manufacturing (3D printing). Each process is chosen based on the complexity of the component, material properties, and production volume.
- Quality Control and Certification: Aerospace component manufacturing requires strict adherence to quality control measures and certification standards such as AS9100 (Aerospace Quality Management System) and NADCAP (National Aerospace and Defense Contractors Accreditation Program). Components undergo rigorous testing and inspection to ensure they meet performance, safety, and reliability criteria.
- Integration and Assembly: Once manufactured, aerospace components are assembled into larger systems and integrated into aircraft or spacecraft. Precision assembly techniques are employed to ensure proper fit, functionality, and performance of the final product.
What are the raw materials for aerospace?
Aerospace manufacturing relies on a diverse range of raw materials to meet the demanding requirements of aircraft and spacecraft construction. Some of the key raw materials include:
- Aluminum Alloys: Aluminum is lightweight yet strong, making it ideal for aircraft structures and components. Alloys such as 2024, 7075, and 6061 are commonly used due to their high strength-to-weight ratio.
- Titanium: Titanium is valued for its exceptional strength, corrosion resistance, and heat resistance. It is often used in critical components like engine parts and structural components.
- Composite Materials: Composites like carbon fiber reinforced polymers (CFRP) and fiberglass are increasingly used in aerospace for their high strength and lightweight properties. These materials offer excellent performance in aircraft components such as fuselages, wings, and interiors.
- Steel Alloys: Certain components in aerospace require the strength and durability of steel alloys. These alloys can withstand high temperatures and mechanical stresses, making them suitable for engine components and landing gear.
- Nickel Alloys: Nickel-based alloys are used in high-temperature applications such as turbine engines due to their excellent heat and corrosion resistance.
- Copper Alloys: Copper alloys like brass and bronze find application in aerospace electrical components and connectors due to their conductivity and corrosion resistance.
- Plastics and Polymers: Various polymers are used for non-structural components in aerospace, including interior panels, ducting, and insulation materials.
- Ceramics: Ceramics are employed in aerospace for specialized applications requiring high temperature resistance, such as thermal barriers and protective coatings.