Vacuum Form Plastic Sheets is a Versatile Solution for Diverse Applications
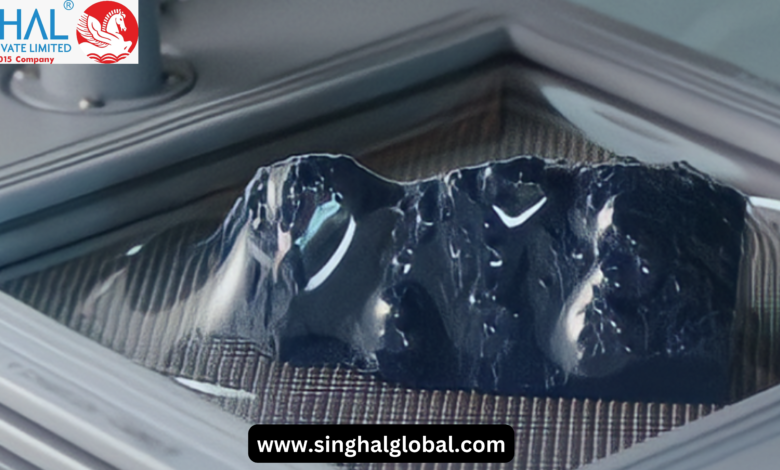
If you’re involved in industries requiring versatile and customizable plastic solutions, you’ve likely encountered the term “vacuum form plastic sheets.” These sheets offer a myriad of benefits, from durability and cost-effectiveness to endless customization possibilities. Let’s delve into the world of Vacuum form plastic sheets, exploring their advantages, applications, and everything in between.
Introduction to Vacuum Form Plastic Sheets
What are vacuum form plastic sheets?
Vacuum form plastic sheets, also known as thermoformed sheets, are thin plastic materials that are heated until pliable and then shaped over a mold using vacuum pressure. This process results in lightweight, yet sturdy, plastic components with a wide range of applications.
Brief history and usage overview
Initially developed in the 1930s, vacuum forming has since evolved into a widely-used manufacturing process across various industries. From automotive interiors to product packaging, vacuum form plastic sheets play a crucial role in modern production methods.
Advantages of Vacuum Form Plastic Sheets
Durability and flexibility
Despite their lightweight nature, vacuum form plastic sheets boast remarkable durability, making them suitable for both indoor and outdoor applications. Additionally, their flexibility allows for complex shapes and designs.
Cost-effectiveness
Compared to traditional manufacturing methods like injection molding, vacuum forming offers significant cost savings, particularly for small to medium production runs. This affordability makes it an attractive option for businesses looking to minimize expenses without sacrificing quality.
Types of Vacuum Form Plastic Sheets
Clear plastic sheets
Ideal for applications requiring transparency, such as display cases or protective covers, clear vacuum form plastic sheets offer excellent optical clarity and UV resistance.
Colored plastic sheets
Available in a spectrum of colors, these sheets are perfect for adding visual appeal to products or creating branded components.
Textured plastic sheets
For enhanced grip or aesthetic purposes, textured vacuum form plastic sheets provide various surface finishes, including matte, gloss, or embossed patterns.
Applications of Vacuum Form Plastic Sheets
Automotive industry
From interior trim components to exterior body panels, vacuum form plastic sheets are widely used in vehicle manufacturing for their lightweight properties and design versatility.
Packaging industry
Vacuum form plastic sheets play a crucial role in product packaging, offering protective enclosures for delicate items while showcasing them attractively to consumers.
Medical field
In medical applications, vacuum form plastic sheets are utilized for equipment housings, surgical trays, and prosthetic devices due to their sterilizability and biocompatibility.
Factors to Consider When Choosing Vacuum Form Plastic Sheets
Material type and thickness
Different plastics offer varying properties, such as impact resistance or chemical compatibility. Additionally, the thickness of the sheet influences its strength and suitability for specific applications.
Size and shape requirements
Whether you need small, intricate components or large, curved surfaces, selecting the right sheet size and shape is crucial for achieving desired outcomes.
Surface finish and texture
Consider the intended use and aesthetics when choosing the surface finish of Vacuum forming plastic sheet suppliers. Options range from smooth and glossy to textured or matte finishes.
Maintenance Tips for Vacuum Form Plastic Sheets
Cleaning and storage guidelines
To prolong the lifespan of vacuum form plastic sheets, regularly clean them with mild soap and water, avoiding abrasive cleaners that may scratch the surface. Store sheets in a cool, dry place away from direct sunlight to prevent warping or discoloration.
Avoiding common issues like warping or yellowing.
Proper handling and storage practices can prevent common issues like warping or yellowing due to prolonged exposure to heat or UV radiation.
Future Trends in Vacuum Form Plastic Sheets
Innovations in material technology.
Advancements in plastic formulations continue to improve the performance and sustainability of vacuum form plastic sheets, with developments in bio-based materials and recyclability leading the way.
Sustainable options and eco-friendly practices.
As environmental concerns grow, there’s a rising demand for sustainable alternatives in plastic manufacturing. Look out for eco-friendly options like biodegradable or recycled plastic sheets.
DIY Vacuum Forming Projects
Hobbyist applications.
With the availability of compact vacuum forming machines, hobbyists and DIY enthusiasts can explore a wide range of creative projects, from custom model-making to cosplay props.
Educational purposes.
Vacuum forming serves as an excellent educational tool for teaching principles of material science, manufacturing processes, and design engineering to students of all ages.
Safety Precautions When Working with Vacuum Forming
Heat-related hazards
Due to the high temperatures involved in the vacuum forming process, proper safety precautions must be taken to prevent burns or other heat-related injuries. Always wear heat-resistant gloves and eye protection when handling heated materials.
Proper ventilation and protective gear
Ensure adequate ventilation in the workspace to dissipate fumes generated during heating. Additionally, wear respiratory protection if working with materials known to emit harmful vapors.
Comparing Vacuum Forming with Other Plastic Forming Techniques
Injection molding
While injection molding offers high precision and consistency, it’s better suited for large-scale production runs and complex geometries. Vacuum forming, on the other hand, is more cost-effective for smaller quantities and simpler shapes.
Thermoforming
Thermoforming encompasses various techniques, including vacuum forming, pressure forming, and twin-sheet forming. Each method has its advantages depending on the specific requirements of the application.
Tips for Buying Vacuum Form Plastic Sheets
Evaluating quality and pricing
When selecting Vacuform plastic sheets, consider factors such as material quality, consistency, and price competitiveness. Request samples or specifications from suppliers to ensure compatibility with your project requirements.
Supplier considerations
Choose reputable suppliers with a proven track record of reliability and customer satisfaction. Look for suppliers who offer customization options, technical support, and timely delivery.
Conclusion
In conclusion, vacuum form plastic sheets offer a versatile and cost-effective solution for a wide range of applications across industries. From automotive components to packaging and medical devices, the benefits of vacuum forming are undeniable. As technology continues to advance, we can expect further innovations in material sustainability and manufacturing efficiency, driving the adoption of vacuum form plastic sheets even further.
FAQs (Frequently Asked Questions)
Are vacuum form plastic sheets recyclable?
While some types of vacuum form plastics are recyclable, it depends on the specific material composition. Check with your local recycling facilities for guidance on proper disposal methods.
Can vacuum form plastic sheets withstand extreme temperatures?
The thermal resistance of vacuum form plastic sheets varies depending on the material type. Some plastics can withstand high temperatures, while others may deform or melt at elevated temperatures.
What are the limitations of vacuum forming?
Vacuum forming is best suited for producing parts with shallow or moderate depth, as deeper draws may result in thinning or stretching of the material. Additionally, complex geometries may require secondary trimming or finishing processes.