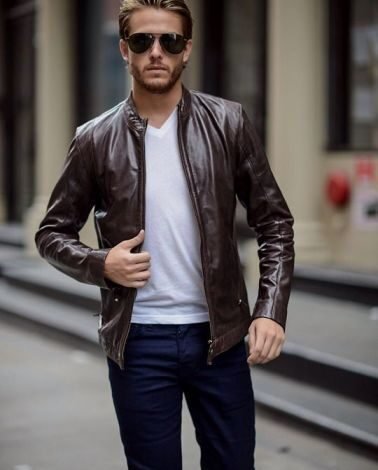
Introduction to FRP Sheets
Fiber-reinforced plastic (FRP) sheets have become increasingly popular in various industries due to their exceptional properties and versatility. These sheets are composed of reinforced fibers embedded in a polymer matrix, resulting in a lightweight yet durable material. Complete Composite Solutions
What are FRP Sheets Made of?
FRP sheets are typically made of a combination of fiberglass and resin. The fiberglass provides strength and rigidity, while the resin acts as a binding agent, holding the fibers together and providing protection against environmental factors. Injection molded shapes
Advantages of FRP Sheets
Durability
One of the key advantages of FRP sheets is their exceptional durability. They are resistant to corrosion, rot, and rust, making them ideal for outdoor applications where exposure to harsh weather conditions is a concern.
Lightweight
Despite their strength, FRP sheets are remarkably lightweight. This makes them easy to handle and install, reducing labor costs and time associated with transportation and handling.
Weather Resistance
FRP sheets exhibit excellent weather resistance, making them suitable for use in outdoor environments. They can withstand prolonged exposure to sunlight, rain, and extreme temperatures without deteriorating or losing their structural integrity.
Common Applications of FRP Sheets
FRP sheets find widespread use across various industries due to their versatility and durability.
Construction Industry
In the construction industry, FRP sheets are commonly used for roofing, wall panels, and structural components. Their lightweight nature and resistance to corrosion make them an ideal choice for both residential and commercial construction projects.
Automotive Sector
In the automotive sector, FRP sheets are utilized for manufacturing vehicle components such as body panels, bumpers, and interior trim. Their high strength-to-weight ratio and impact resistance make them well-suited for enhancing vehicle performance and aesthetics.
Aerospace Industry
The aerospace industry also relies on FRP sheets for manufacturing aircraft components. These sheets offer a combination of lightweight construction and structural integrity, making them essential for aircraft design and manufacturing.
Installation Process of F
The installation process for Fts varies depending on the application and specific requirements. However, it typically involves cutting the sheets to size, pre-drilling holes for fasteners, and securing them in place using adhesive or mechanical fasteners.
Maintenance Tips for FRP Sheets
To ensure the longevity of FRts, proper maintenance is essential. Regular cleaning with mild detergent and water can help remove dirt and debris, while periodic inspection for signs of damage or wear is recommended. Additionally, applying a protective coating can help enhance the weather resistance of FRP sheets.
Cost Considerations
While FRP sheets offer numerous benefits, it’s essential to consider the cost implications. While they may have a higher upfront cost compared to traditional materials, such as steel or wood, their long-term durability and low maintenance requirements can result in cost savings over time.
Environmental Impact of FRP Sheets
FRP sheets have a relatively low environmental impact compared to other materials. They are recyclable and can be repurposed at the end of their lifecycle, reducing the amount of waste sent to landfills. Additionally, their lightweight construction contributes to lower transportation emissions.
Comparing FRP Sheets with Other Materials
When comparing FRP sheets with other materials, such as steel, wood, or aluminum, it’s essential to consider factors such as cost, durability, weight, and environmental impact. While each material has its advantages and limitations, FRP sheets often offer a compelling combination of strength, versatility, and sustainability.
Future Trends in Fet Technology
Looking ahead, ongoing advancements in material science and manufacturing technology are expected to drive further innovation in Ft technology. This includes the development of new reinforcement materials, enhanced manufacturing processes, and improved sustainability practices.
Conclusion
In conclusion, Fts offer a versatile and durable solution for a wide range of applications across various industries. Their lightweight construction, weather resistance, and low maintenance requirements make them an attractive choice for construction, automotive, aerospace, and other sectors. As technology continues to evolve, FRP sheets are likely to play an increasingly important role in shaping the future of material design and manufacturing.
Introduction to Fheets
Fiber-reinforced plastic (ts have become increasingly popular in various industries due to their exceptional properties and versatility. These sheets are composed of reinforced fibers embedded in a polymer matrix, resulting in a lightweight yet durable material.
What are Fts Made of?
Fets are typically made of a combination of fiberglass and resin. The fiberglass provides strength and rigidity, while the resin acts as a binding agent, holding the fibers together and providing protection against environmental factors.
Advantages of Fets
Durability
One of the key advantages of Fets is their exceptional durability. They are resistant to corrosion, rot, and rust, making them ideal for outdoor applications where exposure to harsh weather conditions is a concern.
Lightweight
Despite their strength, Fts are remarkably lightweight. This makes them easy to handle and install, reducing labour costs and time associated with transportation and handling.
Weather Resistance
FRP sheets exhibit excellent weather resistance, making them suitable for use in outdoor environments. They can withstand prolonged exposure to sunlight, rain, and extreme temperatures without deteriorating or losing their structural integrity.
Common Applications of FRP Sheets
FRP sheets find widespread use across various industries due to their versatility and durability.
Construction Industry
In the construction industry, FRP sheets are commonly used for roofing, wall panels, and structural components. Their lightweight nature and resistance to corrosion make them an ideal choice for both residential and commercial construction projects.
Automotive Sector
In the automotive sector, Fets are utilized for manufacturing vehicle components such as body panels, bumpers, and interior trim. Their high strength-to-weight ratio and impact resistance make them well-suited for enhancing vehicle performance and aesthetics.
Aerospace Industry
The aerospace industry also relies on Fts for manufacturing aircraft components. These sheets offer a combination of lightweight construction and structural integrity, making them essential for aircraft design and manufacturing.
Installation Process of F
The installation process for Fts varies depending on the application and specific requirements. However, it typically involves cutting the sheets to size, pre-drilling holes for fasteners, and securing them in place using adhesive or mechanical fasteners.
Maintenance Tips for Fts
To ensure the longevity of Fets, proper maintenance is essential. Regular cleaning with mild detergent and water can help remove dirt and debris, while periodic inspection for signs of damage or wear is recommended. Additionally, applying a protective coating can help enhance the weather resistance of Fts.
Cost Considerations
While Fs offer numerous benefits, it’s essential to consider the cost implications. While they may have a higher upfront cost compared to traditional materials, such as steel or wood, their long-term durability and low maintenance requirements can result in cost savings over time.
Environmental Impact of FRets
Fets have a relatively low environmental impact compared to other materials. They are recyclable and can be repurposed at the end of their lifecycle, reducing the amount of waste sent to landfills. Additionally, their lightweight construction contributes to lower transportation emissions.
Comparing Fts with Other Materials
When comparing Fets with other materials, such as steel, wood, or aluminum, it’s essential to consider factors such as cost, durability, weight, and environmental impact. While each material has its advantages and limitations, FRts often offer a compelling combination of strength, versatility, and sustainability.
Future Trends in FRP Sheet Technology
Looking ahead, ongoing advancements in material science and manufacturing technology are expected to drive further innovation in Ft technology. This includes the development of new reinforcement materials, enhanced manufacturing processes, and improved sustainability practices.
Conclusion
In conclusion, Fts offer a versatile and durable solution for a wide range of applications across various industries. Their lightweight construction, weather resistance, and low maintenance requirements make them an attractive choice for construction, automotive, aerospace, and other sectors. As technology continues to evolve, Fets are likely to play an increasingly important role in shaping the future of material design and manufacturing.