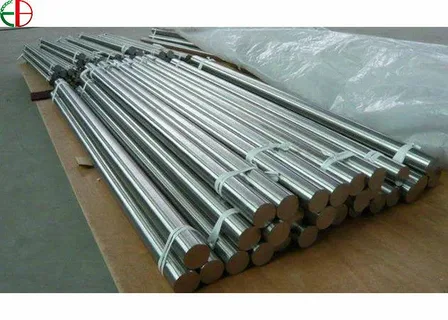
Aircraft Structures:
Titanium Grade 5 wires are extensively utilized in the construction of aircraft structures. From wings and fuselage components to landing gear, the alloy’s lightweight nature contributes to fuel efficiency while maintaining structural integrity. The wires play a crucial role in ensuring the strength and durability of these components.
Engine Components:
Within aircraft engines, the extreme conditions of high temperatures and pressures require materials that can withstand such harsh environments. Titanium Grade 5 wires are used in the manufacturing of engine components such as blades where their high strength and heat resistance prove indispensable.
Manufacturing Process:
The manufacturing of Titanium Grade 5 wires involves a meticulous process to ensure the desired mechanical properties and quality. The alloy undergoes multiple stages of hot and cold working, including extrusion and drawing processes, to achieve the necessary dimensions and surface finish. The wires are then carefully inspected to meet the stringent standards required for aerospace applications.
Role of Titanium Gr 5 Rods:
Titanium Gr 5 Rods, derived from the same alloy, serve as a critical element in aerospace manufacturing alongside wires. These rods, often used interchangeably with wires, find applications in various aerospace components.
Structural Support:
Titanium Gr 5 Rods provide structural support in various aircraft components. Their high strength and lightweight properties make them suitable for creating internal frameworks and support structures within the aircraft, ensuring overall stability and integrity.
Fasteners and Connectors:
In aerospace manufacturing, fasteners and connectors are essential components that require both strength and corrosion resistance. Titanium Gr 5 Rods are frequently used to produce these elements, contributing to the overall reliability and longevity of aerospace systems.
Advantages of Titanium Grade 5 Wires and Rods:
High Strength-to-Weight Ratio:
The exceptional strength-to-weight ratio of Titanium Grade 5 ensures that aerospace components remain robust. without adding unnecessary weight, contributing to fuel efficiency and overall performance.
Corrosion Resistance:
Titanium Grade 5 exhibits excellent corrosion resistance, crucial for aerospace applications where exposure to harsh environmental conditions is inevitable. This property extends the lifespan of components and reduces maintenance requirements.
Heat Resistance:
Aerospace systems often operate in high-temperature environments, especially within aircraft engines. Titanium Grade 5’s ability to withstand elevated temperatures without compromising its structural integrity is a key factor in its selection for critical components.
Challenges and Future Developments:
While Titanium Grade 5 is a highly sought-after material in aerospace manufacturing, challenges such as cost and processing difficulties still exist. Researchers and engineers continue to explore ways to optimize manufacturing processes and reduce production costs, ensuring wider accessibility and application of this remarkable alloy in the aerospace industry. As aerospace technology advances, Titanium Grade 5 continues to be at the forefront of innovation, with ongoing research focused on further enhancing its properties and reducing production costs. The alloy’s compatibility with additive manufacturing processes, such as 3D printing, opens new possibilities for intricate and customized aerospace components.
Additionally, collaborations between material scientists and aerospace engineers are exploring alloy modifications and composite materials to push the boundaries of performance. With its unparalleled combination of strength, weight savings, and corrosion resistance, Titanium Grade 5 wires and Titanium Gr 5 Rods remain at the heart of aerospace manufacturing, contributing to the relentless pursuit of efficiency and safety in the skies.
Unveiling the Aerospace Marvel: Titanium Grade 5 Wires and Rods
In the dynamic realm of aerospace manufacturing, where innovation is the driving force, Titanium Grade 5 has emerged as a cornerstone material, and its wires, along with Titanium Gr 5 Rods, play a central role in shaping the industry’s future.
The Material Marvel: Titanium Grade 5 Properties Revisited
Titanium Grade 5, a titanium alloy comprising 6% aluminum and 4% vanadium. Boasts a unique set of properties that make it an indispensable material in aerospace applications. Its stellar strength-to-weight ratio, corrosion resistance, and ability to withstand extreme temperatures. Made it a preferred choice for manufacturing critical components that demand both durability and precision.
Aerospace Applications: Beyond the Horizon
- Aircraft Structures: Titanium Grade 5 wires weave their magic in the intricate tapestry of aircraft structures. From the wings that gracefully slice through the air to the fuselage components that encapsulate advanced avionics, these wires are integral to ensuring structural integrity while minimizing the overall weight of the aircraft.
- Engine Components: Within the roaring heart of aircraft engines, Titanium Grade 5 wires take on the challenge of withstanding high temperatures and pressures. Blades, discs, and shafts crafted from this alloy contribute to the efficiency and reliability of aerospace propulsion systems.
Manufacturing Mastery: Crafting Titanium Grade 5 Wires
The journey of Titanium Grade 5 from raw material to aerospace marvel involves a meticulous manufacturing process. Hot and cold working techniques, including extrusion and drawing. Are employed to shape the alloy into wires with precise dimensions and surface finishes. Rigorous quality checks are conducted to meet the stringent standards required for aerospace applications, ensuring that each wire meets the exacting demands of the industry.
Enter the Scene: Titanium Gr 5 Rods
In the orchestra of aerospace manufacturing, Titanium Gr 5 Rods take center stage alongside wires. These rods, derived from the same formidable alloy, play a multifaceted role in shaping various aerospace components.
- Structural Support: Titanium Gr 5 Rods provide unseen but vital structural support within aircraft. They form the internal framework, ensuring that the aircraft maintains stability under varying flight conditions. The rods’ high strength ensures the structural integrity of the aerospace systems.
Advantages Amplified: The Superiority of Titanium Grade 5
- High Strength-to-Weight Ratio: The feather-light yet robust nature of Titanium Grade 5 contributes significantly to the fuel efficiency of aircraft. As a critical material in the construction of aerospace components, it ensures that structural strength is achieved without compromising on weight, a paramount factor in aircraft design.
- Corrosion Resistance: Aerospace systems traverse diverse environments, from the piercing heights of the stratosphere to the moisture-laden lower atmospheres. The corrosion-resistant nature of Titanium Grade 5 ensures that aerospace components withstand the test of time. Reducing maintenance requirements and increasing the longevity of critical parts.
- Heat Resistance: Operating within the confines of aircraft engines, where temperatures soar, Titanium Grade 5’s ability to maintain structural integrity under high heat conditions is a game-changer. This property ensures that aerospace systems continue to function optimally even in the most demanding environments.
Challenges and The Path Ahead
While Titanium Grade 5 is undeniably a champion in aerospace materials, challenges persist. Cost considerations and intricate manufacturing processes have limited its widespread use.
Conclusion:
In the ever-evolving landscape of aerospace manufacturing. Titanium Grade 5 wires and Titanium Gr 5 Rods stand out as indispensable materials. Their remarkable properties contribute to the creation of lightweight, durable, and corrosion-resistant components. Ultimately enhancing the safety and efficiency of aerospace systems.