Exploring the Manufacturing Process of Molded Pulp Fiber
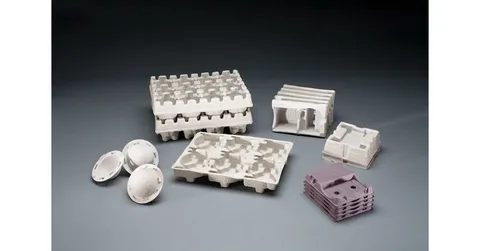
The increasing demand for sustainable materials has brought molded pulp fiber to the forefront as a viable option for eco-friendly packaging. This material, often derived from recycled paper products, is both biodegradable and versatile, making it an ideal choice for industries aiming to reduce their environmental footprint. In this article, we will explore the manufacturing process of molded pulp fiber, focusing on its various stages, advantages, and applications.
1. Introduction to Molded Pulp Fiber
Molded pulp fiber is a biodegradable material made primarily from recycled paper or cardboard. It has gained significant attention in recent years due to its sustainable nature and ability to replace traditional plastic packaging. This fiber-based material can be molded into various shapes, making it suitable for a wide range of products such as trays, containers, and protective packaging.
The production of molded pulp fiber involves several steps, from sourcing raw materials to forming and drying the pulp. Its popularity has soared within industries such as food packaging, electronics, and consumer goods, as it offers an environmentally friendly alternative to plastic products. As consumers and companies alike continue to prioritize sustainability, molded pulp fiber is emerging as a material of choice for reducing waste and conserving natural resources.
2. Sourcing Raw Materials for Molded Pulp Fiber
The first step in the manufacturing process of molded pulp fiber involves sourcing raw materials. Typically, these materials include recycled paper, cardboard, or other cellulose fibers. The choice of raw materials is crucial, as it directly impacts the quality and properties of the final product. The fibers must be thoroughly cleaned and processed to remove any impurities or contaminants before being used in the pulp-making process.
Once the raw materials are sourced, they undergo a pulping process in which they are broken down into fine fibers using water and mechanical forces. The pulp is then tested for consistency, fiber length, and quality to ensure it meets the required standards for molding. Recycled paper and cardboard are favored due to their sustainability, as they divert waste from landfills and reduce the need for virgin materials, making molded pulp fiber an environmentally friendly option from the outset.
3. The Pulping Process
After raw materials are sourced and prepared, the next step in the molded pulp fiber manufacturing process is pulping. This process involves breaking down the raw fibers into a slurry by mixing them with water. During pulping, mechanical forces, such as grinding or beating, are applied to separate the fibers from one another and create a smooth, consistent pulp.
The consistency of the pulp is critical, as it needs to be neither too thick nor too thin. The ideal pulp should be fluid enough to flow easily into molds but thick enough to hold its shape during the molding process. Various chemicals can be added during pulping to improve the strength or color of the molded pulp fiber. After pulping, the slurry is then filtered and refined to remove any large particles or debris, ensuring the pulp is smooth and uniform for molding.
4. Molding and Shaping the Pulp Fiber
Once the pulp is prepared, it is poured into molds where it takes on its final shape. Molding is one of the most important steps in the production of molded pulp fiber, as it defines the final form of the product. The molds can be designed for a variety of products, such as trays, protective packaging, or even custom-designed containers. The pulp is poured or sprayed into the molds, and then vacuum or pressure is applied to remove excess water and help the material conform to the shape of the mold.
This stage also involves the use of heat or air drying to remove any remaining moisture from the pulp. The drying process can vary depending on the size and complexity of the molded pulp product. Products made from molded pulp fiber are often lightweight yet strong, making them suitable for a wide range of uses. After the shaping and drying process, the molded pulp fiber products are carefully inspected for any defects or inconsistencies.
5. Finishing and Quality Control
The final stage in the production of molded pulp fiber involves finishing and quality control. After the molded pulp products have been dried and shaped, they undergo a series of inspections to ensure they meet quality standards. This includes checking for structural integrity, proper dimensions, and overall aesthetic appearance. Any defects or inconsistencies are addressed before the products are packaged and ready for shipment.
In addition to visual inspection, some manufacturers may perform additional tests on the molded pulp fiber to assess its strength, moisture resistance, and durability. If the product is intended for use in food packaging or other sensitive applications, it may also undergo safety testing to ensure it is free from harmful chemicals or contaminants. Once the products pass all quality control checks, they are packaged and distributed to customers for use in a variety of industries.
Conclusion
The manufacturing process of molded pulp fiber is a detailed and multi-step procedure that transforms raw recycled materials into a versatile, eco-friendly product. From sourcing raw materials to the final finishing touches, each stage plays a vital role in ensuring the quality and functionality of the molded pulp fiber. As more industries turn to sustainable alternatives, molded pulp fiber is poised to play a significant role in reducing the reliance on plastic products and promoting a more sustainable future. Through innovations in manufacturing processes and continuous improvements in material quality, molded pulp fiber is set to become an even more essential component of environmentally conscious packaging solutions.