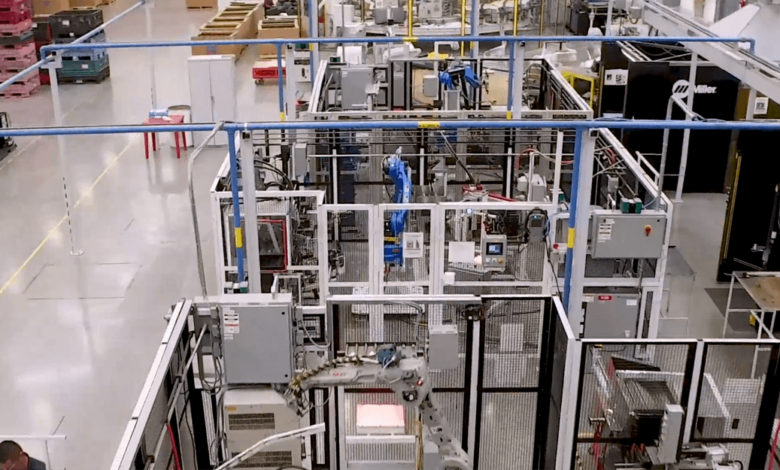
In today’s manufacturing landscape, efficiency and precision are paramount. Injection moulding machines have emerged as a cornerstone technology, transforming the way various industries produce goods. Let’s delve into the intricacies of injection moulding machine, exploring their significance, functionality, and impact on modern manufacturing.
Defining Injection Moulding Machines
Injection moulding machines are advanced manufacturing tools utilized to fabricate intricate parts by injecting molten material into a mould. This process enables the mass production of products with consistent quality and intricate designs.
Importance and Relevance
The significance of injection moulding machines lies in their ability to streamline production processes, reduce manufacturing costs, and enhance product quality. From automotive components to consumer electronics, these machines play a pivotal role in diverse industries worldwide.
Types and Categories
Injection moulding machines come in various types and configurations to cater to different manufacturing needs. Let’s explore the primary categories:
Hydraulic Injection Moulding Machine
Hydraulic machines utilize hydraulic power to generate the necessary force for moulding. These machines are renowned for their high clamping force and are ideal for large-scale production.
Electric Injection Moulding Machine
Electric machines leverage electric motors for moulding operations, offering precise control and energy efficiency. They are favored for their accuracy and repeatability.
Hybrid Injection Moulding Machines
Hybrid machines combine hydraulic and electric components, offering the benefits of both technologies. They strike a balance between power and efficiency, making them versatile solutions for various applications.
Symptoms and Signs
Identifying the need for injection moulding machine involves recognizing specific symptoms and signs:
Increased Production Demands
Rising production demands necessitate the adoption of efficient manufacturing technologies like injection moulding machines to meet consumer needs promptly.
Quality Control Challenges
Quality issues such as inconsistencies in product dimensions or surface defects signal the need for advanced moulding solutions to ensure consistent quality.
Cost Inefficiencies
Traditional manufacturing methods may incur high production costs due to material wastage or lengthy cycle times, highlighting the need for cost-effective alternatives like injection moulding.
Causes and Risk Factors
Several factors drive the adoption of injection moulding machine in manufacturing environments:
Technological Advancements
Continuous advancements in injection moulding technology have led to the development of highly efficient and versatile machines, enticing manufacturers to upgrade their production capabilities.
Market Competition
Intense competition in the global market compels manufacturers to enhance their operational efficiency and product quality, prompting the adoption of cutting-edge technologies like injection moulding.
Environmental Concerns
Growing awareness of environmental sustainability encourages the use of eco-friendly manufacturing processes, with injection moulding machines offering energy-efficient and recyclable solutions.
Diagnosis and Tests
Determining the suitability of injection moulding machine for specific manufacturing requirements involves comprehensive diagnosis and testing:
Material Compatibility
Assessing the compatibility of raw materials with injection moulding processes is crucial to ensure optimal results and prevent material degradation or defects.
Mould Design Analysis
Conducting thorough analysis and simulations of mould designs helps identify potential issues and optimize the moulding process for maximum efficiency and quality.
Performance Testing
Performing rigorous performance tests on injection moulding machines evaluates their precision, reliability, and production capacity, ensuring seamless integration into manufacturing workflows.
Treatment Options
Once the need for injection moulding machines is established, various treatment options are available to address manufacturing challenges:
Procurement and Installation
Procuring suitable injection moulding machines tailored to specific production requirements and installing them with precision ensures smooth operation and optimal performance.
Operator Training and Skill Development
Providing comprehensive training programs for operators enhances their proficiency in operating injection moulding machines, minimizing errors and maximizing productivity.
Maintenance and Calibration
Regular maintenance and calibration of injection moulding machines prevent downtime and ensure consistent output quality, prolonging the lifespan of equipment and reducing production costs.
Preventive Measures
Implementing preventive measures is essential to mitigate potential risks and optimize the performance of injection moulding machines:
Routine Inspections
Regular inspections of equipment components, including screws, barrels, and heating elements, help identify wear and tear early and prevent costly breakdowns.
Temperature and Pressure Control
Maintaining precise temperature and pressure control during the moulding process ensures optimal material flow and prevents defects such as warping or sink marks.
Process Optimization
Continuously optimizing injection moulding parameters, such as injection speed and cooling time, maximizes efficiency and product quality while minimizing production waste.
Personal Stories or Case Studies
Real-life experiences and case studies illustrate the tangible impact of injection moulding machine on manufacturing operations:
Case Study: Automotive Industry
A leading automotive manufacturer implemented injection moulding machines to fabricate complex interior components, significantly reducing production time and costs while improving product durability.
Personal Story: Small Business Success
A small-scale electronics manufacturer shares their journey of adopting injection moulding technology, highlighting how it transformed their business by enabling rapid prototyping and customization.
Expert Insights
Industry experts offer valuable insights into the benefits and challenges of using injection moulding machine:
Dr. Emily Chen, Materials Engineer
“Injection moulding machine revolutionize manufacturing by offering unparalleled precision and efficiency. However, it’s crucial for manufacturers to invest in quality equipment and prioritize proper maintenance to maximize returns.”
John Davis, Production Manager
“The versatility of injection moulding machines allows us to cater to diverse customer demands while maintaining consistent quality standards. Continuous innovation in machine design and materials expands our capabilities and drives business growth.”
Conclusion
Injection moulding machines represent a cornerstone technology in modern manufacturing, offering unmatched precision, efficiency, and versatility. By understanding their significance, functionality, and best practices for implementation and maintenance, manufacturers can unlock new opportunities for growth and innovation in their respective industries.
FAQs
1. How can I learn more about Windsor Machines’ products and services? Visit Windsor Machines’ official website or contact their sales team for more information and personalized assistance.
2. Does Windsor Machines offer financing options for its products? Yes, Windsor Machines provides flexible financing options to help businesses acquire the equipment they need while managing their cash flow effectively.
3. Can Windsor Machines’ solutions be integrated with existing production systems? Yes, Windsor Machines’ solutions are designed to seamlessly integrate with existing production systems, minimizing disruption and maximizing efficiency.
4. What sets Windsor Machines apart from other manufacturing equipment suppliers? Windsor Machines’ dedication to innovation, quality, and customer satisfaction sets it apart as a trusted partner for businesses seeking to optimize their manufacturing operations.
5. How can I get in touch with Windsor Machines’ customer support team? For assistance with technical issues, maintenance inquiries, or general questions, customers can contact Windsor Machines’ customer support team through their website or by phone.