Knowing the Value of Ramming Mass and How to Use It in Industrial Furnaces
Knowing the Value of Ramming Mass and How to Use It in Industrial Furnaces
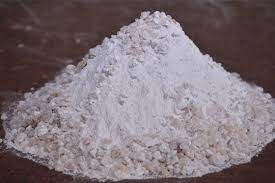
Introduction:
In order to ensure the longevity and effectiveness of industrial furnaces, ramming mass is an essential part of their construction and maintenance. The complexities, significance, and industrial applications of ramming mass are discussed in detail in this article.
What is Mass Ramming?
Ramming mass is a refractory lining material used to line arc furnaces, induction furnaces, and other high-temperature applications. It is sometimes referred to as ramming mix or refractory ramming mass. Refractory aggregates and a bonding agent—typically a high-temperature binder like silica or alumina—make up its composition.
The significance of ramping mass
Thermal Insulation: By preventing heat escape, ramming mass helps to maintain the ideal temperature inside the furnace.
Erosion Resistance: It prolongs the furnace’s life by shielding the interior lining from the erosive impacts of molten metal and slag.
Thermal Stability: Consistent furnace operation is ensured by the structural integrity of ramming mass, even in the face of high temperature variations.
Application Ease: Because of its flexibility, maintenance expenses and downtime are decreased by the ease of installation and repair.
Cost Efficiency: Over time, ramming mass reduces costs by prolonging the lifespan and efficiency of furnaces.
Utilizing Ramming Mass:
Ramming mass is used to line the walls and bottom of induction furnaces, where it endures the extreme heat produced during the melting and casting of metal.
Arc Furnaces: Ramming mass is applied as a protective lining against the high temperatures and corrosive substances in arc furnaces used to make steel environment created by molten metal and slag.
Foundries: Ramming material is used to line molds and crucibles in foundries, which creates ideal conditions for the casting of metal.
Non-Ferrous Metal Industry: It is used in smelting processes and furnaces that process non-ferrous metals such as copper, zinc, and aluminum.
In conclusion,
ramming mass is essential to the dependable and effective operation of industrial furnaces in a variety of industries. Because of its resistance to erosion, thermal insulating qualities, and ease of application, it is a material that is essential for preserving furnace integrity and maximizing output. The necessity for high-quality ramming mass endures because industries that depend on high-temperature processes need to ensure both cost-effectiveness and operational efficiency.