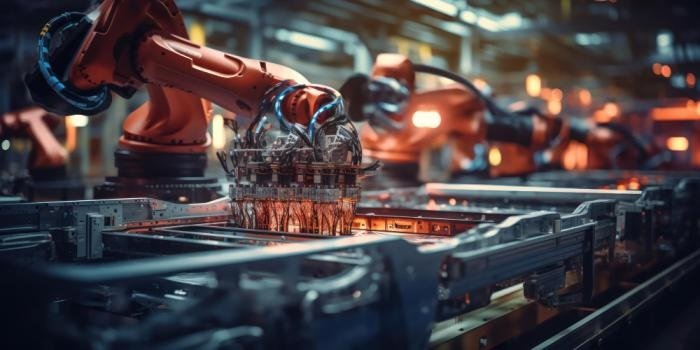
In the rapidly evolving landscape of manufacturing, leveraging advanced technology has become imperative for staying competitive. The integration of manufacturing IT solutions not only reduces costs but also enhances product features, quality, and production efficiency. This article explores various IT solutions that are transforming the manufacturing sector, highlighting their roles in cost reduction and feature enhancement.
Introduction
The manufacturing industry has witnessed significant transformations driven by technological advancements. From the Industrial Revolution to the current era of Industry 4.0, each phase has introduced new tools and methodologies that redefine production processes. Today, the convergence of information technology (IT) and manufacturing, known as manufacturing IT solutions, is ushering in a new age of smart factories, where data, connectivity, and automation play pivotal roles.
The Role of Manufacturing IT Solutions
Manufacturing IT solutions encompass a broad range of technologies designed to streamline operations, enhance product quality, and reduce costs. These solutions include:
- Enterprise Resource Planning (ERP) Systems
- Manufacturing Execution Systems (MES)
- Industrial Internet of Things (IIoT)
- Artificial Intelligence (AI) and Machine Learning (ML)
- Robotic Process Automation (RPA)
- Additive Manufacturing (3D Printing)
- Digital Twin Technology
- Supply Chain Management (SCM) Systems
Each of these technologies contributes uniquely to the efficiency and effectiveness of manufacturing processes.
Enterprise Resource Planning (ERP) Systems
ERP systems are comprehensive software platforms used to manage and integrate the core business processes of an organization. In manufacturing, ERP systems provide several benefits:
Cost Reduction
- Resource Optimization: ERP systems help manufacturers optimize resource use by providing real-time data on inventory, production schedules, and supply chain activities. This reduces wastage and lowers operational costs.
- Improved Forecasting: With accurate demand forecasting, manufacturers can reduce excess inventory and avoid stockouts, leading to cost savings.
- Streamlined Operations: ERP systems integrate various departments, such as finance, HR, and procurement, into a unified system, reducing administrative overhead and improving operational efficiency.
Feature Enhancement
- Customization: Modern ERP systems offer modular architectures, allowing manufacturers to customize functionalities according to their specific needs.
- Real-Time Analytics: Advanced analytics capabilities enable manufacturers to gain insights into production processes, enhancing decision-making and product development.
Manufacturing Execution Systems (MES)
MES are IT solutions that monitor and control manufacturing operations on the factory floor. They act as a bridge between ERP systems and the actual production processes.
Cost Reduction
- Operational Efficiency: MES provide real-time visibility into production activities, helping to identify bottlenecks and inefficiencies quickly.
- Reduced Downtime: By monitoring machine performance and predicting maintenance needs, MES can significantly reduce unplanned downtime.
- Quality Control: MES ensure that production processes adhere to defined quality standards, reducing waste and rework costs.
Feature Enhancement
- Traceability: MES provide detailed tracking of materials and products through the manufacturing process, enhancing traceability and compliance with regulatory standards.
- Enhanced Collaboration: By integrating with other IT systems, MES facilitate better collaboration among different departments, leading to improved product features and innovation.
Industrial Internet of Things (IIoT)
The IIoT refers to the use of internet-connected devices and sensors in industrial applications. In manufacturing, IIoT solutions enable real-time data collection and analysis from machinery and production lines.
Cost Reduction
- Predictive Maintenance: IIoT devices can predict equipment failures before they occur, reducing maintenance costs and preventing costly downtime.
- Energy Efficiency: Real-time monitoring of energy consumption helps identify inefficiencies and optimize energy use, lowering utility bills.
- Inventory Management: IIoT-enabled smart inventory systems track materials and products in real time, reducing holding costs and improving inventory turnover.
Feature Enhancement
- Smart Manufacturing: IIoT facilitates the creation of smart factories where machinery and processes are interconnected, leading to higher automation levels and improved product features.
- Enhanced Product Quality: Continuous monitoring and feedback loops ensure that products meet stringent quality standards, enhancing customer satisfaction.
Artificial Intelligence (AI) and Machine Learning (ML)
AI and ML technologies are increasingly being integrated into manufacturing processes to analyze data, optimize operations, and drive innovation.
Cost Reduction
- Process Optimization: AI algorithms can optimize production schedules, reducing idle times and improving throughput.
- Defect Detection: ML models can analyze images and data to detect defects early in the production process, reducing scrap and rework costs.
- Supply Chain Optimization: AI helps optimize supply chain logistics, reducing transportation and warehousing costs.
Feature Enhancement
- Product Development: AI-driven insights can accelerate product development cycles, leading to innovative features and faster time-to-market.
- Customization: AI enables mass customization by analyzing customer preferences and adapting production processes to meet specific demands.
Robotic Process Automation (RPA)
RPA involves the use of software robots to automate repetitive and mundane tasks in manufacturing.
Cost Reduction
- Labor Costs: RPA reduces the need for manual labor in repetitive tasks, leading to significant cost savings.
- Operational Efficiency: By automating routine tasks, RPA increases the speed and accuracy of operations, reducing errors and associated costs.
Feature Enhancement
- Scalability: RPA systems can be easily scaled up or down according to production needs, providing flexibility in manufacturing processes.
- Enhanced Accuracy: Automation ensures high precision in tasks, improving the overall quality of products.
Additive Manufacturing (3D Printing)
Additive manufacturing, commonly known as 3D printing, involves creating three-dimensional objects by adding material layer by layer based on digital models.
Cost Reduction
- Material Efficiency: 3D printing minimizes material wastage compared to traditional subtractive manufacturing processes.
- Tooling Costs: The need for specialized tooling is reduced, lowering initial setup costs.
- Prototyping: Rapid prototyping capabilities allow for quick and cost-effective testing of product designs.
Feature Enhancement
- Complex Designs: 3D printing enables the production of complex and intricate designs that are difficult to achieve with traditional manufacturing methods.
- Customization: Manufacturers can produce customized products tailored to individual customer requirements without significant cost increases.
Digital Twin Technology
Digital twins are virtual replicas of physical assets, systems, or processes. They are used to simulate, analyze, and optimize manufacturing operations.
Cost Reduction
- Predictive Maintenance: Digital twins enable continuous monitoring and simulation of machinery, predicting failures and reducing maintenance costs.
- Process Optimization: By simulating production processes, digital twins help identify inefficiencies and optimize workflows, reducing operational costs.
Feature Enhancement
- Enhanced Design: Digital twins facilitate virtual testing and validation of new designs, leading to better product features and reduced time-to-market.
- Real-Time Monitoring: They provide real-time insights into production processes, enabling dynamic adjustments and improvements.
Supply Chain Management (SCM) Systems
SCM systems manage the flow of goods, information, and finances across the supply chain network. Advanced SCM solutions leverage technologies like blockchain, AI, and IoT.
Cost Reduction
- Inventory Optimization: SCM systems provide real-time visibility into inventory levels, reducing carrying costs and minimizing stockouts.
- Logistics Efficiency: By optimizing transportation routes and schedules, SCM systems reduce shipping costs and delivery times.
- Supplier Management: Enhanced supplier collaboration and performance monitoring lead to better procurement terms and reduced costs.
Feature Enhancement
- Traceability: SCM systems enhance traceability and transparency across the supply chain, ensuring compliance with quality and regulatory standards.
- Customer Satisfaction: Improved supply chain coordination leads to timely delivery of products, enhancing customer satisfaction and loyalty.
Integrating IT Solutions for Maximum Impact
The true potential of manufacturing IT solutions is realized when they are integrated seamlessly. An integrated approach ensures that data flows smoothly between different systems, providing a holistic view of manufacturing operations. Here are some strategies for successful integration:
Data Integration
- Unified Data Platform: Implement a unified data platform that consolidates data from various IT systems, providing a single source of truth.
- Interoperability: Ensure that different IT solutions are interoperable, using standard protocols and APIs for seamless data exchange.
Process Integration
- Workflow Automation: Automate workflows across different systems to streamline processes and reduce manual intervention.
- Cross-Functional Collaboration: Foster collaboration between different departments by integrating IT systems that support communication and information sharing.
Continuous Improvement
- Feedback Loops: Establish feedback loops to continuously monitor and improve manufacturing processes based on real-time data insights.
- Scalability: Choose scalable IT solutions that can grow with your business and adapt to changing manufacturing needs.
Conclusion
Leveraging manufacturing IT solutions is no longer optional but a necessity for staying competitive in today’s dynamic market. By integrating advanced technologies such as ERP, MES, IIoT, AI, RPA, 3D printing, digital twins, and SCM systems, manufacturers can significantly reduce costs and enhance product features. The key to maximizing the benefits of these solutions lies in seamless integration, data-driven decision-making, and a commitment to continuous improvement. As the manufacturing landscape continues to evolve, those who embrace and leverage these IT solutions will be well-positioned to lead the industry forward.