Magnetic Separators in the Food Industry: Ensuring Product Purity and Safety
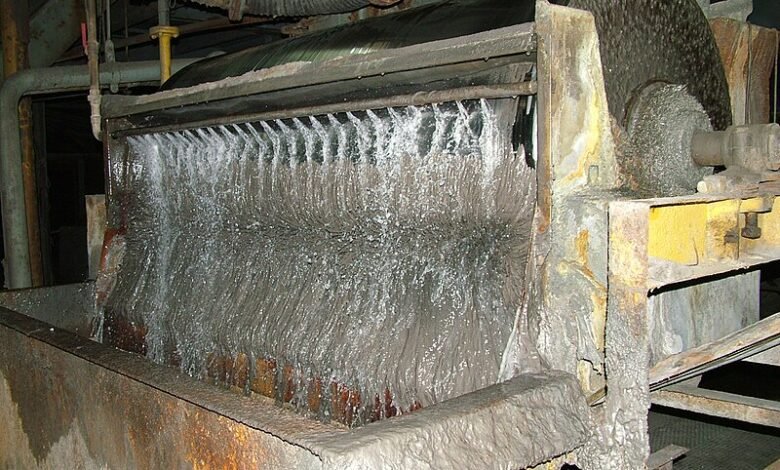
The food industry is one of the most critical sectors where purity and safety are paramount. Contaminants, especially metal particles, can severely affect product quality and pose health risks. A key player in ensuring the highest safety standards is the use of Magnetic Separators. These devices are designed to remove metal contaminants from food products, protecting both consumers and food processors from potentially harmful substances.
The Importance of Purity in Food Production
Ensuring product purity is a central focus in the food industry. Contaminants, such as metal shavings, rust, or fragments from machinery, can find their way into food during various stages of production. These particles can cause significant harm to both the consumer and the brand’s reputation. Therefore, it is crucial to incorporate robust systems, such as Magnetic Separators, into food production lines to prevent contamination at the source.
Food manufacturers are constantly under pressure to meet safety regulations and provide high-quality products. Magnetic separation offers a reliable solution by removing any ferrous and non-ferrous metals, which are common contaminants. These separators ensure that the food is free from potentially harmful substances, contributing to the industry’s efforts to maintain food safety and quality standards.
How Magnetic Separators Work in Food Processing
Magnetic Separators use powerful magnets to attract metal particles from food products. These separators are strategically installed along production lines, where they help detect and remove metal contaminants from raw materials, semi-finished products, or even finished goods. The magnetic field generated by the separator pulls metals such as iron, steel, and other magnetic materials, which could otherwise contaminate the food.
Different types of magnetic separators are used depending on the nature of the product and the level of contamination. Some separators work in dry processing, while others are designed for wet food applications. Regardless of the method, these devices are vital in preventing the risk of metal-related injuries to consumers or damage to machinery.
Types of Magnetic Separators in the Food Industry
There are several types of Magnetic Separators employed in the food industry, each tailored to specific needs and food types. The most common include:
- Plate Magnets: Often installed in chutes or conveyors, plate magnets attract metals as they pass through the food production line.
- Liquid Line Traps: These separators are ideal for food products in liquid form, such as juices or sauces, where metal contamination may be harder to detect.
- Hopper Magnets: Placed in hoppers or silos, these magnets help ensure that any metals in bulk ingredients are removed before they are processed further.
Each of these separators plays a crucial role in maintaining food safety standards. By selecting the appropriate magnetic separation system, food manufacturers can ensure the complete removal of metal contaminants, providing higher-quality products to the market.
Benefits of Magnetic Separation in Food Safety
Magnetic separators provide numerous benefits to the food industry. The most immediate advantage is the prevention of metal contamination, which can cause severe injury to consumers or machinery. By incorporating Magnetic Separators into production lines, food manufacturers reduce the risk of contamination, which in turn decreases the likelihood of recalls, lawsuits, and damaged reputations.
Moreover, these separators help improve the efficiency of production. By eliminating metal contaminants early in the process, magnetic separators prevent blockages and wear-and-tear on machines, reducing maintenance costs and downtime. This leads to smoother operations and more consistent product quality.
Magnetic separation also contributes to compliance with industry regulations. Food safety standards often require manufacturers to implement metal detection systems, and magnetic separators help meet these obligations by providing an effective method for contamination removal.
Integrating Magnetic Separators into Food Production Lines
The integration of Magnetic Separators into food production lines can significantly enhance safety and efficiency. For optimal performance, it’s essential that manufacturers understand the different stages of production and identify where contamination risks are highest. By doing so, they can strategically place magnetic separators at key points in the production line.
Regular maintenance and cleaning of magnetic separators are also essential to ensure their continued effectiveness. Over time, the magnets may lose their power or become clogged with debris, reducing their ability to attract and remove metal particles. Scheduled inspections and maintenance are vital to maintaining the integrity of the food safety system.
Cost-Effectiveness and Return on Investment
While the initial investment in Magnetic Separators may seem significant, the long-term benefits far outweigh the costs. By preventing metal contamination, manufacturers avoid the costs associated with product recalls, legal liabilities, and damaged customer trust. Additionally, the reduction in machine maintenance and downtime provides a substantial return on investment.
Moreover, magnetic separation systems often have a long lifespan, with minimal maintenance required. This makes them an economical choice for food processors looking to enhance safety and operational efficiency. Over time, the savings generated by preventing contamination-related issues and optimizing production outweigh the initial costs of installation.
Food Industry Standards and Compliance
In the food industry, compliance with strict safety standards is essential for maintaining consumer trust and avoiding costly legal issues. The Food and Drug Administration (FDA), the European Food Safety Authority (EFSA), and other regulatory bodies set guidelines for metal contamination and food safety. Magnetic Separators help food manufacturers meet these guidelines by ensuring that food products are free from harmful metal contaminants.
By integrating these separators into their processes, manufacturers demonstrate a commitment to quality and safety, adhering to the best practices in food processing. This not only ensures the safety of the end product but also enhances the overall reputation of the brand.
Conclusion
Magnetic separators play a pivotal role in ensuring product purity and safety in the food industry. From preventing metal contamination to improving operational efficiency, these devices are an essential part of modern food production lines. The adoption of Magnetic Separators not only protects consumers but also enhances the efficiency and reliability of production operations.
By investing in high-quality magnetic separation systems, food manufacturers can safeguard their products, improve their compliance with safety standards, and ultimately build trust with consumers. As the food industry continues to evolve, magnetic separators will remain a key technology in maintaining the highest safety standards and ensuring the purity of every product.