Plastic Granules Manufacturing Plant Project Report 2024: Required Materials and Setup
Plastic Granules Manufacturing Plant Project Report
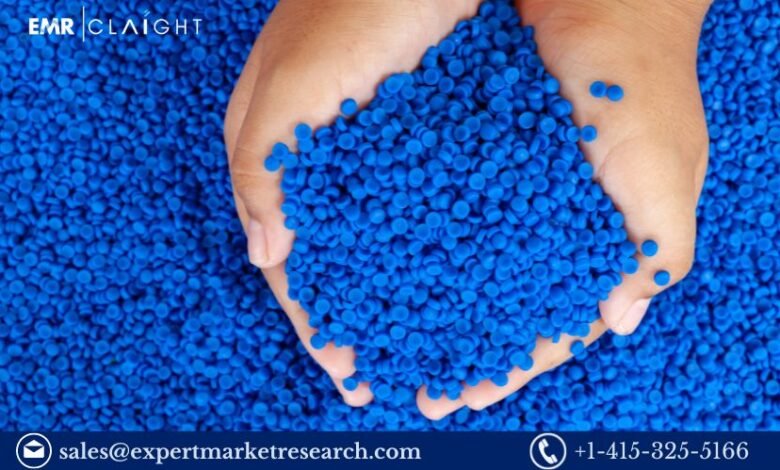
Introduction
Plastic granules are small plastic pellets used as raw materials in various industries, including packaging, automotive, electronics, and construction. The increasing demand for plastic products, driven by urbanization and changing consumer preferences, presents a lucrative opportunity for establishing a plastic granules manufacturing plant. This Plastic Granules Manufacturing Plant Project Report outlines the critical aspects of setting up such a facility, including market analysis, raw materials, production processes, equipment requirements, and financial considerations.
Market Overview
The global plastic granules market is experiencing robust growth, fueled by several factors:
- Increasing Plastic Demand: Plastics are widely used due to their versatility, durability, and cost-effectiveness. Industries such as packaging, automotive, and consumer goods are significant contributors to the demand for plastic granules.
- Sustainability Trends: With the rising awareness of environmental concerns, there is a growing demand for recycled plastic granules. This trend presents an opportunity for manufacturers to produce eco-friendly products.
- Technological Advancements: Innovations in polymer processing technologies are enhancing the efficiency of plastic production, enabling manufacturers to meet evolving market needs.
- Economic Growth: As economies develop, the demand for plastic products increases, further driving the need for plastic granules.
Get a Free Sample Report with Table of Contents @
Project Overview
1. Location Selection
Selecting an appropriate location for the manufacturing plant is crucial for operational efficiency. Key factors to consider include:
- Proximity to Raw Material Suppliers: Being near suppliers of plastic resins, additives, and other raw materials can reduce transportation costs.
- Infrastructure: Access to utilities such as water, electricity, and transportation networks is essential for smooth operations.
- Regulatory Environment: The location must comply with local environmental and safety regulations regarding plastic manufacturing.
2. Raw Materials
The primary raw materials required for producing plastic granules include:
- Polymer Resins: The most commonly used resins include polyethylene (PE), polypropylene (PP), polyvinyl chloride (PVC), and polystyrene (PS). The choice of resin depends on the intended application of the granules.
- Additives: Various additives may be included to enhance the properties of the granules, such as colorants, stabilizers, plasticizers, and fillers.
- Recycled Plastics: Incorporating recycled materials can help reduce production costs and contribute to sustainability efforts.
3. Manufacturing Process
The manufacturing process for plastic granules typically involves several key steps:
Step-by-Step Manufacturing Process:
- Material Preparation: Raw materials, including polymer resins and additives, are sourced, weighed, and prepared for processing.
- Mixing: The resin and additives are mixed in specific proportions to achieve the desired properties. This step is critical for ensuring uniformity.
- Extrusion: The mixed materials are fed into an extruder, where they are heated and melted. The molten plastic is then forced through a die to form continuous strands.
- Cooling: The extruded strands are cooled using water baths or air cooling systems to solidify the material.
- Cutting: Once cooled, the strands are cut into small granules of uniform size.
- Quality Control: Rigorous quality control tests are conducted to ensure the granules meet industry standards. Tests may include checking for size consistency, color accuracy, and material properties.
- Packaging: The final plastic granules are packaged in bags or containers for distribution.
4. Machinery and Equipment
Setting up a plastic granules manufacturing plant requires specific machinery and equipment, including:
- Extruders: These machines are essential for melting and shaping the plastic resins into strands.
- Cooling Systems: Equipment for cooling the extruded strands to solidify the material.
- Cutting Machines: Devices for cutting the cooled strands into granules of the desired size.
- Mixers: Machines for blending the resin and additives before extrusion.
- Quality Control Instruments: Instruments for testing the properties of the granules, ensuring they meet specifications.
Investing in high-quality equipment can enhance production efficiency and product quality.
Financial Considerations
1. Capital Investment
Establishing a plastic granules manufacturing plant requires significant capital investment. Key areas of expenditure include:
- Land and Infrastructure: Costs associated with purchasing land and constructing manufacturing facilities that comply with safety and regulatory standards.
- Machinery and Equipment: The purchase of extruders, cooling systems, cutting machines, and mixers represents a significant investment.
- Working Capital: Funds are needed for initial raw material purchases, labor costs, and operational expenses.
2. Operational Costs
Operational costs will include:
- Raw Materials: Expenses related to sourcing polymer resins, additives, and other necessary materials.
- Labor Costs: Salaries for skilled and unskilled workers involved in the manufacturing process.
- Utilities: Expenses for electricity, water, and other essential services.
- Maintenance: Ongoing maintenance costs for machinery and equipment.
Effective cost management strategies, such as negotiating bulk purchase agreements and optimizing production processes, can enhance profitability.
3. Revenue and Profitability
Revenue generation will depend on production capacity, product pricing, and market demand. The plastic granules manufacturing business can be profitable, especially if the plant can produce high-quality products at competitive prices.
Factors influencing profitability include:
- Market Demand: Understanding and adapting to market trends can help align production with consumer needs.
- Product Quality: Ensuring high-quality products can lead to repeat customers and establish a strong market reputation.
- Cost Efficiency: Reducing production costs through process optimization and efficient resource management can improve profit margins.
FAQs
1. What are plastic granules?
Plastic granules are small plastic pellets used as raw materials in various industries, including packaging, automotive, and consumer goods.
2. What raw materials are needed for plastic granule production?
The primary raw materials include polymer resins (such as polyethylene, polypropylene, and PVC) and various additives to enhance properties.
3. What is the manufacturing process for plastic granules?
The process involves material preparation, mixing, extrusion, cooling, cutting, quality control, and packaging.
4. What challenges might be faced when establishing a plastic granules manufacturing plant?
Challenges may include sourcing quality raw materials, adhering to regulatory requirements, managing operational costs, and ensuring consistent product quality.
5. How can a plastic granules manufacturing plant ensure profitability?
Profitability can be achieved by optimizing production efficiency, maintaining high product quality, adapting to market trends, and effectively managing costs.
Related Reports
https://www.expertmarketresearch.com/articles/top-5-companies-in-the-global-banana-flakes-market
https://www.expertmarketresearch.com/articles/top-sodium-cocoyl-isethionate-companies
https://www.expertmarketresearch.com/reports/acetic-acid-market
Media Contact:
Company Name: Claight Corporation
Contact Person: Lewis Fernandas, Corporate Sales Specialist — U.S.A.
Email: sales@expertmarketresearch.com
Toll Free Number: +1–415–325–5166 | +44–702–402–5790
Address: 30 North Gould Street, Sheridan, WY 82801, USA
Website: www.expertmarketresearch.com
Aus Site: https://www.expertmarketresearch.com.au