Business
The Art of Custom Silk Screen Printing on Shirts / Clothes
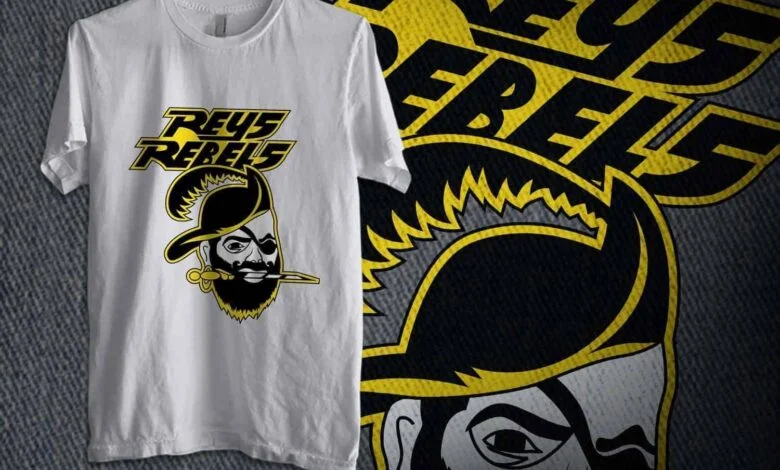
Silk screen printing, also known as screen printing or serigraphy, is a versatile and time-honored method for printing designs on various surfaces, including shirts. This process involves transferring ink through a mesh screen onto the shirt, creating vibrant and durable prints. In this comprehensive guide, we will explore the intricate process of silk screen printing on shirts, covering each step from design preparation to the final product, while delving into equipment, materials, and best practices for achieving professional results.
Understanding Silk Screen Printing:
- Silk screen printing is a stencil-based printing technique that dates back centuries. Traditionally, silk was used as the mesh material for the screen, hence the name. However, modern screens are typically made from polyester or nylon. The process involves creating a stencil on the screen and using a squeegee to force ink through the mesh onto the shirt, transferring the design.
Design Preparation:
- The silk screen printing process begins with the preparation of the design to be printed. Designs can be created digitally or hand-drawn and then transferred onto a transparent film or stencil material. Each color in the design requires a separate stencil, so multi-color designs need multiple screens.
Screen Preparation:
- Once the design is finalized, it’s time to prepare the screens. Screens are coated with a light-sensitive emulsion, which is exposed to UV light through the stencil. The areas of the emulsion exposed to light harden, while the areas covered by the stencil remain soft and can be washed away, creating the stencil for the design.
Printing Process:
- With the screens prepared, the printing process can begin. Here’s how it works:
- Positioning: The shirt is placed on a flat surface, and the screen is aligned over the printing area.
- Ink Application: Ink is poured onto the screen, and a squeegee is used to spread it evenly across the stencil, forcing it through the mesh onto the shirt.
- Multiple Colors: For designs with multiple colors, each color requires a separate pass with a different screen and ink color. Careful registration is essential to ensure accurate alignment of colors.
Curing:
- After printing, the ink needs to be cured to ensure durability and wash-fastness. This is typically done by passing the printed shirts through a conveyor dryer, where they are exposed to high temperatures for a specific amount of time. Curing the ink bonds it to the fabric fibers, creating a lasting print.
Quality Control:
- Throughout the printing process, operators monitor the print quality and make adjustments as needed to ensure consistent results. Each printed shirt undergoes thorough inspection to check for any defects, misprints, or inconsistencies. Quality control measures help to ensure that the final product meets the desired standards of clarity and durability.
Post-Processing:
- Once the printing and curing are complete, any excess ink or residue is removed from the shirts. The shirts may undergo post-processing steps such as steaming or pressing to further enhance the appearance and feel of the print. Finally, the shirts are folded, labeled, and packaged for distribution or retail sale.