The Benefits of Rubber Design Bellows: A Comprehensive Overview
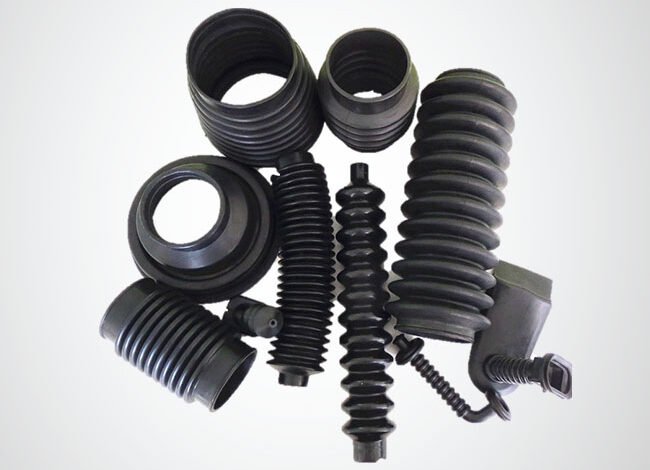
Rubber design bellows are essential components in various industries, providing flexibility, protection, and durability for machinery and equipment. These versatile elements are designed to accommodate movement, absorb vibrations, and seal against contaminants, making them indispensable in numerous applications. This article explores the numerous benefits of rubber design bellows, highlighting their impact on machinery performance, safety, and maintenance.
What Are Rubber Design Bellows?
Definition and Purpose
Rubber design bellows are flexible, expandable components made from rubber or elastomeric materials. They are engineered to absorb and manage movement, protect machinery from contaminants, and enhance the longevity of equipment. The primary functions of bellows include:
- Accommodating Movement: They can expand, contract, and flex to accommodate shifts in machinery alignment and position.
- Protecting Components: Bellows shield sensitive parts from dust, dirt, moisture, and other environmental factors.
- Absorbing Vibrations: They help reduce vibrations and shocks, ensuring smoother operation and less wear on machinery.
Key Characteristics
- Flexibility: Rubber bellows are designed to flex and stretch, adapting to changes in machinery.
- Durability: Constructed from high-quality rubber, they offer excellent resistance to wear and environmental conditions.
- Sealing Capability: Bellows provide effective sealing to prevent the ingress of contaminants.
Benefits of Rubber Design Bellows
Enhanced Machinery Protection
One of the primary benefits of rubber design bellows is their ability to protect machinery and components:
- Contaminant Protection: Bellows create a barrier against dust, dirt, and moisture, preventing these contaminants from damaging sensitive parts.
- Corrosion Prevention: By keeping contaminants away, bellows help prevent rust and corrosion on metal components, extending their lifespan.
- Reduced Wear and Tear: Protection from external factors reduces the likelihood of wear and tear on machinery, leading to fewer repairs and replacements.
Improved Performance and Efficiency
Rubber bellows contribute to better performance and efficiency in machinery:
- Reduced Vibration: By absorbing vibrations and shocks, bellows help maintain the stability and precision of machinery, enhancing overall performance.
- Smooth Operation: The flexibility of bellows allows for smooth operation by accommodating movements and adjustments in machinery, reducing operational stress.
- Increased Longevity: Proper protection and reduced wear contribute to longer-lasting equipment, minimizing downtime and maintenance costs.
Versatility and Adaptability
Rubber design bellows are highly versatile and adaptable to various applications:
- Customizable Designs: Bellows can be designed in various shapes, sizes, and configurations to meet specific application requirements.
- Wide Range of Applications: They are used in automotive, industrial, aerospace, medical, and many other fields, demonstrating their broad applicability.
- Adaptability to Conditions: Rubber bellows can be engineered to withstand different environmental conditions, including extreme temperatures and exposure to chemicals.
Cost-Effectiveness
Investing in rubber design bellows can be cost-effective in the long run:
- Reduced Maintenance Costs: By protecting machinery and reducing wear, bellows lower maintenance and repair expenses.
- Extended Equipment Life: Bellows help extend the life of equipment by providing reliable protection and reducing the need for frequent replacements.
- Efficient Operation: Improved performance and efficiency lead to better overall operational costs, making bellows a valuable investment.
Enhanced Safety
Safety is a critical consideration in the use of rubber design bellows:
- Protecting Operators: By preventing the ingress of contaminants and ensuring smooth operation, bellows help maintain a safer working environment for operators.
- Reducing Failures: Reliable protection reduces the risk of equipment failures and associated safety hazards, contributing to a safer workplace.
- Compliance with Standards: Many rubber bellows are designed to meet industry standards and regulations, ensuring they contribute to overall safety compliance.
Applications of Rubber Design Bellows
Rubber bellows are used across various industries, each benefiting from their unique properties:
Automotive Industry
In the automotive sector, rubber bellows are crucial for:
- Suspension Systems: Bellows protect suspension components from dirt and moisture, ensuring smooth and reliable operation.
- Engine Seals: They seal around engine parts, preventing contaminants from causing damage and maintaining optimal performance.
- Vibration Absorption: Rubber bellows absorb vibrations and shocks, enhancing ride comfort and vehicle stability.
Industrial Machinery
Industrial applications benefit from rubber bellows in several ways:
- Covering Actuators: Bellows protect linear actuators and other moving parts from debris and environmental factors, extending their lifespan.
- Sealing Machinery: They seal moving parts in machinery, preventing the ingress of dust and contaminants that could cause malfunctions.
- Accommodating Movement: Rubber bellows handle movements and expansions in machinery, reducing stress and ensuring efficient operation.
Aerospace and Defence
In aerospace and defence applications, rubber bellows play a vital role in:
- Sealing Aircraft Components: Bellows provide effective seals for various aircraft components, ensuring reliable performance under extreme conditions.
- Managing Pressure Changes: They accommodate pressure changes in aerospace systems, maintaining system integrity and functionality.
- Protecting Sensitive Equipment: Rubber bellows shield sensitive equipment from environmental factors, ensuring reliability and safety.
Medical Devices
Rubber bellows are essential in the medical field for:
- Sealing Medical Equipment: They seal medical devices to prevent contamination and ensure hygienic conditions.
- Managing Movement: Bellows handle movement in medical machinery, such as pumps and valves, enhancing precision and reliability.
- Absorbing Vibrations: They help absorb vibrations in medical devices, ensuring accurate measurements and smooth operation.
Factors to Consider When Selecting Rubber Design Bellows
When choosing rubber design bellows, several factors must be considered:
Application Requirements
Identify the specific requirements of your application:
- Movement Type: Determine the type and extent of movement the bellows need to accommodate, such as axial, angular, or radial.
- Environmental Conditions: Assess environmental factors like temperature, pressure, and exposure to chemicals that may impact the bellows.
Material Selection
Select a material that matches your application needs:
- Temperature Resistance: Choose a material that can withstand the operating temperature.
- Chemical Resistance: Opt for a material that resists chemicals and solvents if exposure is a concern.
- Flexibility Requirements: Select a material with the required flexibility and elasticity for your application.
Design Specifications
Consider design features that will affect performance:
- Shape and Size: Ensure the bellows are the correct shape and size for your application to ensure proper fit and functionality.
- Reinforcement: Determine if internal reinforcement, such as fabric or wire mesh, is needed for added strength.
- End Fittings: Select end fittings that match your attachment requirements to ensure a secure and effective seal.
Installation and Maintenance
Proper installation and maintenance are crucial for optimal performance:
Installation Tips
- Alignment: Ensure proper alignment during installation to prevent misalignment and premature wear.
- Secure Attachment: Use appropriate clamps or fittings to secure the bellows and maintain a proper seal.
- Avoid Overstretching: Install the bellows without overstretching to prevent damage and ensure optimal functionality.
Maintenance Practices
Regular maintenance helps extend the life of rubber bellows:
- Inspection: Regularly inspect bellows for signs of wear, damage, or leaks. Check for cracks, tears, or deformation.
- Cleaning: Keep bellows clean and free from debris. Use mild detergents and avoid abrasive cleaning methods.
- Replacement: Replace bellows that show significant wear or damage to prevent failures and maintain system efficiency.
Future Trends in Rubber Design Bellows
Advances in Materials
Innovations in materials are enhancing the performance and durability of rubber bellows:
- Advanced Elastomers: New elastomer materials offer improved resistance to extreme temperatures, chemicals, and wear.
- Composite Materials: Composite materials provide enhanced strength and flexibility for demanding applications.
Technological Integration
Emerging technologies are integrating with rubber bellows to enhance functionality:
- Sensors and Monitoring: Integration of sensors for real-time monitoring of bellows performance and condition.
- Smart Materials: Development of smart materials that respond to environmental changes, improving adaptability and performance.
Conclusion
Rubber design bellows offer a wide range of benefits, including enhanced machinery protection, improved performance, versatility, cost-effectiveness, and safety. By understanding their features, applications, and selection criteria, you can make informed decisions to ensure optimal performance and longevity. Proper installation and maintenance are essential for maximizing the benefits of rubber bellows, while staying informed about advancements in materials and technology will help you make the best choices for your applications. Rubber design bellows continue to play a vital role in enhancing machinery efficiency and ensuring safety across diverse industries.