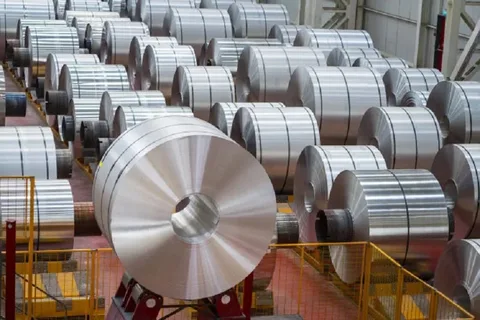
Introduction:
Welding stainless steel coils, particularly those made of the resilient 347H variant, demands precision, expertise, and an understanding of the unique properties of this alloy. While welding stainless steel is already a nuanced task, 347H coils present their own set of challenges and considerations. In this guide, we’ll delve into the best practices for welding stainless steel 347H coils, offering insights and tips to help you achieve optimal results.
Understanding Stainless Steel 347H Coils:
Stainless steel 347H is a high carbon, niobium-stabilized austenitic stainless steel, specifically designed for elevated temperature service. Its composition offers excellent resistance to intergranular corrosion, as well as good mechanical properties at high temperatures. These coils are widely used in various industries, including chemical processing, petrochemical, and pharmaceutical sectors, where they encounter harsh operating conditions.
Best Practices for Welding Stainless Steel 347H Coils:
Pre-Weld Preparation:
Before initiating the welding process, thorough cleaning and preparation of the stainless steel surface are crucial. Remove any contaminants, such as oil, grease, or oxides, using solvents or mechanical methods. Additionally, ensure the coils are properly aligned and securely clamped to prevent distortion during welding.
Selecting the Right Filler Material:
The choice of filler material significantly influences the quality and integrity of the weld. For welding stainless steel 347H coils, opt for filler metals with matching or slightly overmatching composition to maintain corrosion resistance and mechanical properties. Common choices include AWS A5.9 ER347 and ER347H filler wires.
Controlled Heat Input:
Given the susceptibility of stainless steel 347H to sensitization and intergranular corrosion, controlling heat input during welding is paramount. Utilize low heat input welding techniques, such as TIG (Tungsten Inert Gas) or GTAW (Gas Tungsten Arc Welding), to minimize the heat-affected zone (HAZ) and mitigate the risk of carbide precipitation.
Back Purging:
To safeguard the weld area from oxidation and ensure the integrity of the weld joint, implement back purging with inert gas (e.g., argon) during welding. This prevents the formation of chromium carbides along the grain boundaries, preserving the corrosion resistance of the stainless steel.
Post-Weld Treatment:
After completing the welding process, undertake proper post-weld treatment to alleviate residual stresses and enhance the mechanical properties of the weld. Annealing or solution heat treatment followed by water quenching can help restore the alloy’s microstructure and improve its toughness and ductility.
Preheating:
In scenarios where the coils are subjected to high levels of restraint or thickness, consider preheating the base material to reduce the risk of cracking and improve weldability. Preheating to temperatures between 200°C to 400°C helps lower the cooling rate, minimizing the formation of martensite and reducing the likelihood of hydrogen-induced cracking.
Interpass Temperature Control:
Maintain strict control over interpass temperatures during multi-pass welding to prevent overheating and potential degradation of the material’s properties. Monitor and limit the maximum interpass temperature to prevent excessive grain growth and maintain the desired microstructure.
Weld Joint Design:
Opt for appropriate weld joint designs, such as single or double V-groove configurations, to ensure sufficient penetration and fusion throughout the weld joint. Proper joint preparation and fit-up are essential to facilitate smooth welding operations and achieve sound, defect-free welds.
Avoiding Contamination:
Exercise caution to prevent contamination of the weld zone by refractory metals, such as tungsten from the welding electrode in TIG welding. Maintain a consistent welding technique and ensure adequate shielding gas coverage to minimize the risk of tungsten inclusions or contamination that could compromise weld integrity.
Post-Weld Inspection:
Conduct thorough visual and non-destructive testing (NDT) inspections, such as dye penetrant testing (PT) or radiographic testing (RT), to assess weld quality and detect any defects or discontinuities. Address any identified flaws promptly through appropriate repair procedures to uphold the integrity of the weld and ensure compliance with industry standards.
Shielding Gas Composition:
Pay close attention to the composition of the shielding gas used during welding. Employing high-purity argon or argon-rich mixtures can help minimize the risk of contamination and ensure optimal weld cleanliness. Avoid using shielding gases containing hydrogen, which can induce hydrogen embrittlement in the weld metal.
Controlled Welding Parameters:
Maintain strict control over welding parameters, including voltage, current, travel speed, and arc length, to achieve consistent weld bead geometry and mechanical properties. Fine-tune these parameters based on the specific requirements of the application and the characteristics of stainless steel 347H to optimize weld quality and performance.
Post-Weld Heat Treatment:
In certain applications, especially those involving heavy sections or critical service conditions, consider performing post-weld heat treatment (PWHT) to relieve residual stresses and enhance the overall integrity of the welded structure. Controlled heating and cooling cycles tailored to the material’s composition can help refine the microstructure and minimize the risk of stress corrosion cracking.
Avoidance of Distortion:
Take proactive measures to mitigate distortion and warping of the stainless steel coils during welding. Employ techniques such as intermittent welding, tack welding, or the use of clamping and fixturing devices to minimize the effects of thermal expansion and contraction. Additionally, consider employing welding sequences that distribute residual stresses evenly across the structure to prevent distortion.
Training and Qualification:
Invest in comprehensive training and qualification programs for welders involved in welding stainless steel 347H coils. Ensure that welders are proficient in the specific techniques and procedures required for welding this material, and conduct periodic assessments to verify their competency and adherence to quality standards.
Documentation and Traceability:
Maintain detailed documentation of welding procedures, welder qualifications, and inspection records to ensure traceability and compliance with regulatory requirements. Establish a robust quality management system that tracks every stage of the welding process, from material procurement to final inspection, to uphold the highest standards of quality and accountability.
Environmental Controls:
Pay attention to environmental factors that could affect the welding process and the quality of the weld. Ensure adequate ventilation and control of humidity levels in the welding area to prevent the formation of surface contaminants or atmospheric pollutants that could compromise weld integrity.
Joint Preparation and Fit-Up:
Prioritize meticulous joint preparation and fit-up to facilitate optimal weld penetration and fusion. Use appropriate bevel angles and root openings to ensure full joint penetration and promote efficient welding deposition. Employ techniques such as back gouging or grinding to achieve clean, uniform joint profiles.
Dynamic Welding Techniques:
Consider employing dynamic welding techniques, such as oscillation or weaving patterns, to enhance weld uniformity and mechanical properties. Controlled oscillation of the welding torch or manipulator can help distribute heat evenly across the weld zone, reducing the likelihood of distortion and promoting consistent fusion.
Material Handling and Storage:
Ensure stainless steel 347H coil integrity with correct material handling and storage practices before, during, and after the welding process. Preserve coil integrity by storing in a clean, dry area, away from contaminants, and using proper lifting equipment to avoid damage.
Post-Weld Cleaning:
After completing welding operations, conduct thorough post-weld cleaning to remove any residual flux, slag, or spatter from the weld area. Utilize appropriate cleaning methods, such as wire brushing, grinding, or chemical cleaning, to achieve a smooth, uniform surface finish and enhance the aesthetics and corrosion resistance of the weld.
Documentation and Reporting:
Ensure compliance with industry standards and customer requirements by maintaining detailed documentation of welding procedures, material certifications, and quality control. Generate detailed welding reports that capture essential parameters and observations, facilitating traceability and accountability throughout the fabrication process.
Continuous Improvement:
Foster a culture of continuous improvement within your welding operations, encouraging feedback, innovation, and knowledge sharing among team members. Regularly review welding procedures, performance metrics, and customer feedback to identify opportunities for optimization and refinement.
Conclusion:
Welding stainless steel 347H coils demands meticulous attention to detail and adherence to specialized techniques. Optimize welding techniques for durable stainless steel 347H components, ensuring superior quality and performance in challenging environments. Embrace these expert tips, elevate your welding proficiency, and unlock the full potential of this versatile alloy.