Exploring Linear Actuators: Versatile Solutions for Motion Control
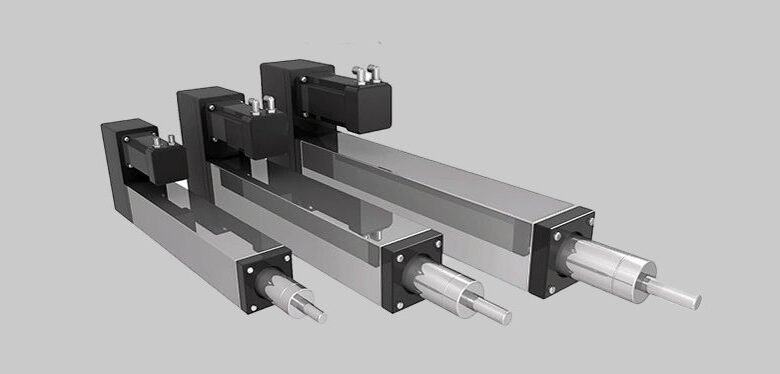
Linear actuators are fundamental components in various industries, enabling precise linear motion in machinery, robotics, automotive systems, and more. This article provides an in-depth exploration of linear actuators, covering their types, applications, working principles, advantages, and technological advancements.
1. **Introduction to Linear Actuators**
Linear actuators are devices designed to convert rotary motion into linear motion, facilitating the movement of components along a straight path. They are essential for achieving controlled and precise displacement in mechanical systems, offering versatility in both industrial and consumer applications.
2. **Types of Linear Actuators**
Linear actuators come in different types, each suited to specific applications:
Mechanical Actuators:
Simple mechanisms like screws or cams convert rotational motion into linear motion.
Hydraulic Actuators:
Use pressurized hydraulic fluid to generate linear force, ideal for heavy-duty applications.
Pneumatic Actuators:
Utilize compressed air to produce linear motion, offering quick response and ease of control.
Electric Actuators:
Directly convert electrical energy into linear motion, with options like:
Lead Screw Actuator:
Transforms rotary motion into linear motion using a screw mechanism.
Linear Motor Actuators:
Utilizes electromagnetic principles for precise and rapid linear movement.
Each type has unique advantages in terms of force output, speed, precision, and environmental suitability.
3. **Applications Across Industries**
Linear actuators find widespread use in various sectors due to their adaptability and reliability:
dustrial Automation:
Positioning components on assembly lines and robotic systems.
Medical Devices:
Precision movement in surgical robots and diagnostic equipment.
Aerospace:
Adjusting control surfaces and landing gear mechanisms.
Automotive:
Actuating valves, throttle controls, and convertible roof mechanisms.
Home Automation:
Adjusting furniture, solar panels, and ventilation systems.
Their ability to provide controlled linear motion enhances efficiency, safety, and performance across diverse applications.
4. **Working Principles**
The working principle of linear actuators varies based on their type:
Electric Actuators**: Convert electrical energy into linear motion through mechanisms like lead screws or linear motors.
Hydraulic Actuators**: Use hydraulic pressure to move a piston, generating linear force proportional to the fluid pressure.
Pneumatic Actuators**: Utilize compressed air to move a piston or diaphragm, translating air pressure into linear motion.
Mechanical Actuators**: Employ mechanical means such as screws, belts, or cams to achieve linear displacement.
Understanding these principles helps in selecting the appropriate actuator for specific operational requirements.
5. **Advantages of Linear Actuators**
Linear actuators offer several benefits compared to traditional motion mechanisms:
Precision: Achieve accurate positioning and movement control.
Compact Design: Space-efficient solutions suitable for constrained environments.
Quiet Operation: Electric and some mechanical actuators operate silently.
Maintenance: Require minimal upkeep compared to hydraulic or pneumatic systems.
Customizability: Options for integrating feedback sensors and control systems for automated operation.
These advantages contribute to improved operational efficiency and reduced downtime in various applications.
6. **Technological Advancements**
Recent advancements in linear actuators have expanded their capabilities and functionalities:
Integrated Electronics: Actuators with built-in controllers for precise motion control.
Smart Actuators: IoT-enabled actuators capable of remote monitoring and control.
High-Speed Actuators: Increased efficiency and faster response times.
Materials and Coatings: Enhanced durability and performance in harsh environments.
Energy Efficiency: Designs optimized for reduced power consumption and heat dissipation.
These advancements cater to evolving industry demands for higher performance, reliability, and sustainability.
7. **Considerations for Selection**
Choosing the right linear actuator involves considering several factors:
Load Capacity: Ensure the actuator can handle the required force and weight.
Speed and Stroke Length: Match the speed and stroke capabilities to application requirements.
Environmental Conditions: Select actuators with appropriate ingress protection and resistance to temperature extremes.
Control Interface: Compatibility with existing control systems and protocols.
Cost and Lifecycle: Balance initial investment with long-term operational costs and reliability.
Careful consideration of these factors ensures optimal performance and longevity of the selected linear actuator.
8. **Future Trends**
Looking ahead, several trends are shaping the future of linear actuators:
Miniaturization: Smaller actuators for compact applications and wearable technology.
Artificial Intelligence: AI-driven actuators for predictive maintenance and adaptive control.
Advanced Materials: Lightweight and durable materials for improved performance.
Human-Robot Collaboration: Actuators designed for safe interaction in collaborative robotics.
Energy Harvesting: Actuators that recover and reuse energy for sustainable operation.
These trends indicate a continued evolution towards smarter, more efficient, and environmentally friendly linear actuator solutions.
Conclusion
Linear actuators play a pivotal role in modern technology by enabling precise linear motion across a wide range of applications. Their versatility, combined with advancements in design and technology, continues to drive innovation in industries from manufacturing and healthcare to aerospace and beyond. By understanding the types, applications, working principles, advantages, and future trends of linear actuators, engineers and decision-makers can harness their capabilities to enhance productivity, efficiency, and competitiveness in a rapidly evolving global market.
Embracing these advancements ensures that linear actuators remain indispensable tools for achieving controlled linear motion and unlocking new possibilities in automation, robotics, and beyond.