Precision Engineering: Excellence in PTFE Tube Fitting
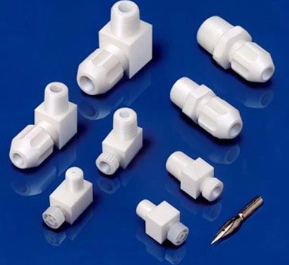
In the intricate world of fluid handling systems, precision engineering stands as the cornerstone of reliability, efficiency, and safety. Among the array of components essential for seamless fluid transfer, PTFE (Polytetrafluoroethylene) tube fittings exemplify the pinnacle of engineering excellence. These fittings, meticulously crafted with precision and expertise, play a pivotal role in ensuring leak-free connections, optimal performance, and longevity in diverse industrial applications. Let’s delve into the fascinating realm of precision engineering in PTFE tube fitting and uncover the factors that contribute to their engineering superiority.
Meticulous Design and Manufacturing Processes:
Precision engineering in PTFE tube fittings begins with meticulous design and manufacturing processes that prioritize accuracy, consistency, and quality. Engineers leverage advanced CAD (Computer-Aided Design) software and simulation tools to conceptualize and refine intricate designs, optimizing functionality and performance. Through precise machining techniques such as CNC (Computer Numerical Control) machining and EDM (Electrical Discharge Machining), manufacturers translate these designs into meticulously crafted components with tight tolerances and exact specifications.
Tight Tolerances and Dimensional Accuracy:
At the heart of precision engineering in PTFE tube fittings lies the adherence to tight tolerances and dimensional accuracy. Each component, from the fitting body to the ferrule and nut, is manufactured to precise tolerances, ensuring seamless compatibility and interlocking functionality. By maintaining strict dimensional accuracy, PTFE tube fittings guarantee secure, leak-free connections, even in high-pressure and high-temperature environments.
Material Selection and Properties:
The choice of materials is critical in precision engineering, and PTFE tube fittings excel in this regard. PTFE, known for its exceptional chemical resistance, low friction coefficient, and non-stick properties, serves as the ideal material for fluid handling applications. Engineers carefully select high-quality PTFE resins with specific properties tailored to withstand the demands of harsh operating conditions, ensuring durability, reliability, and longevity.
Sealing Mechanisms and Leak Prevention:
Precision engineering in PTFE tube fittings extends to the design of sealing mechanisms aimed at preventing leaks and ensuring fluid integrity. Double-ferrule compression fittings, commonly used in PTFE tube fitting assemblies, feature a unique twin-ferrule design that creates a robust, leak-tight seal. This innovative design distributes the sealing forces evenly, minimizing the risk of leaks and enhancing the overall reliability of the fluid system.
Quality Assurance and Testing Protocols:
Throughout the manufacturing process, rigorous quality assurance and testing protocols are employed to validate the precision and performance of PTFE tube fittings. From dimensional inspections and surface finish analysis to pressure testing and leak detection, each fitting undergoes comprehensive testing to ensure compliance with industry standards and specifications. By upholding stringent quality standards, manufacturers uphold the integrity and reliability of PTFE tube fittings, instilling confidence in their performance in critical applications.
Advanced Surface Treatments and Coatings:
In addition to precise machining and material selection, advanced surface treatments and coatings further enhance the performance and longevity of PTFE tube fittings. Techniques such as passivation, electroplating, and PTFE coating are employed to improve surface finish, corrosion resistance, and wear resistance. These treatments not only protect the fittings from environmental factors and chemical exposure but also facilitate smoother fluid flow and reduce the risk of fouling or buildup.
Customization and Tailored Solutions:
Precision engineering in PTFE tube fittings extends beyond standardization to offer customized solutions tailored to specific application requirements. Engineers collaborate closely with clients to understand their unique challenges and design fittings that meet exact specifications, including special configurations, sizes, and performance parameters. This customization ensures optimal functionality and compatibility with existing systems, maximizing efficiency and minimizing downtime.
Innovative Connection Technologies:
As technology evolves, precision engineering in PTFE tube fitting drives innovation in connection technologies, offering solutions that address emerging challenges and requirements. For example, push-to-connect fittings leverage advanced locking mechanisms to simplify installation and reduce assembly time, while maintaining the precision and reliability characteristic of traditional compression fittings. Similarly, quick-connect fittings enable rapid disconnection and reconnection for maintenance or system reconfiguration, without compromising on sealing integrity or performance.
Integration of Smart Features:
With the advent of Industry 4.0 and IoT (Internet of Things) technologies, precision-engineered PTFE tube fitting are increasingly incorporating smart features for enhanced functionality and predictive maintenance capabilities. Sensors embedded within fittings enable real-time monitoring of pressure, temperature, and flow rates, providing valuable insights into system performance and condition. This proactive approach to maintenance minimizes downtime, reduces costs, and optimizes the efficiency of fluid handling systems.
Lifecycle Assessment and Sustainability Considerations:
Precision engineering in PTFE tube fitting encompasses a holistic approach that extends beyond performance. To consider environmental sustainability throughout the product lifecycle. Engineers conduct lifecycle assessments to evaluate the environmental impact of materials, manufacturing processes, and end-of-life disposal options. By optimizing designs for recyclability, minimizing waste generation, and reducing energy consumption. Manufacturers ensure that PTFE tube fittings align with sustainable development goals and contribute to a greener future.
Pressure Rating Optimization:
Precision engineering in PTFE tube fittings involves optimizing pressure ratings to ensure compatibility with specific operating conditions and applications. Engineers carefully calculate and design fittings to withstand varying levels of pressure, taking into account factors such as fluid type, temperature. And system requirements. By accurately determining pressure ratings and selecting appropriate materials. And construction techniques, PTFE tube fittings can reliably perform under high-pressure environments without compromising safety or integrity.
Thermal Stability and Heat Dissipation:
PTFE tube fittings undergo precision engineering to enhance thermal stability and heat dissipation properties. Crucial for applications involving elevated temperatures or thermal cycling. Engineers design fittings with features such as heat sinks, thermal barriers. And optimized geometries to minimize heat transfer and prevent thermal degradation. This ensures that PTFE tube fittings maintain their performance and integrity. Even in demanding thermal conditions, preserving system efficiency and reliability over time.
Fatigue and Stress Analysis:
Precision engineering in PTFE tube fittings includes thorough fatigue and stress analysis to assess. The structural integrity and durability of components under varying load conditions. Engineers utilize finite element analysis (FEA) and computational fluid dynamics (CFD) simulations to model stress distribution. Identify potential failure points, and optimize designs to minimize fatigue-related issues such as cracking. Deformation, or material fatigue. This meticulous analysis ensures that PTFE tube fittings can withstand long-term. Operation without experiencing premature failure or performance degradation.
Compliance with Industry Standards and Regulations:
Precision-engineered PTFE tube fittings are designed and manufactured to comply with stringent industry standards and regulations governing fluid handling systems. Engineers ensure that fittings meet specifications set forth by organizations such as ASTM International. ASME (American Society of Mechanical Engineers), and ANSI (American National Standards Institute). As well as regulatory requirements imposed by government agencies and safety authorities. Compliance with these standards ensures that PTFE tube fittings meet quality, safety, and performance benchmarks. Instilling confidence in their reliability and suitability for use in critical applications.
Continuous Improvement and Innovation:
Precision engineering in PTFE tube fittings involves a commitment to continuous improvement. And innovation to address evolving challenges and customer needs. Engineers collaborate with research and development teams to explore new materials, manufacturing techniques. And design concepts that push the boundaries of performance, efficiency, and sustainability. By embracing innovation and staying at the forefront of technological advancements, manufacturers ensure that PTFE tube fittings. Remain at the cutting edge of fluid handling solutions, delivering value and reliability to customers across industries.
Conclusion:
Precision engineering is the bedrock of excellence in PTFE tube fittings, ensuring uncompromising quality. Reliability, and performance in fluid handling systems. Through meticulous design, manufacturing processes, tight tolerances. Material selection, sealing mechanisms, and rigorous testing protocols, engineers elevate PTFE tube fittings to the pinnacle of engineering excellence. As essential components in diverse industries ranging from chemical processing. Pharmaceuticals to aerospace and automotive, PTFE tube fittings demonstrate the profound impact of precision engineering. On the reliability and efficiency of fluid handling systems.